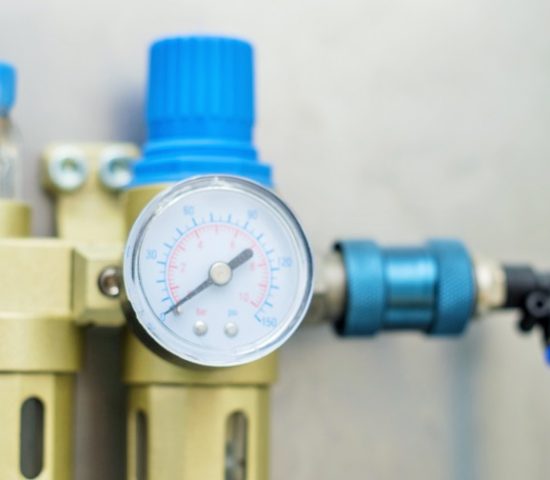
PRØVNING AF RENHEDSKLASSE
FOR TRYKLUFT
[ISO 8573-1]
- Indhold af partikler
- Vandindhold / trykdugpunkt
- Indhold af olieaerosol
- Mikrobiologiske undersøgelser (indhold af bakterier, gær og skimmelsvampe)
ISO 8573-1 er en bredt accepteret standard, der anvendes til at klassificere trykluftens renhed baseret på indholdet af tre forurenende stoffer: faste partikler, vand og olie. Prøveudtagningsmetoderne og selve målingerne er beskrevet i detaljer i de efterfølgende afsnit i ISO 8573 (-2, -3, -4), og deres anvendelse er obligatorisk, når målet er at sammenligne de opnåede måleresultater med de i ISO 8573-1 beskrevne renhedsklasser for trykluft. I nogle industrier testes trykluft også for mikrobiologiske forureninger; disse tests danner dog ikke grundlag for ISO 8573-1-klassificeringen af renhedsklassen for trykluft, men supplerer den kun.
ISO 8573-1
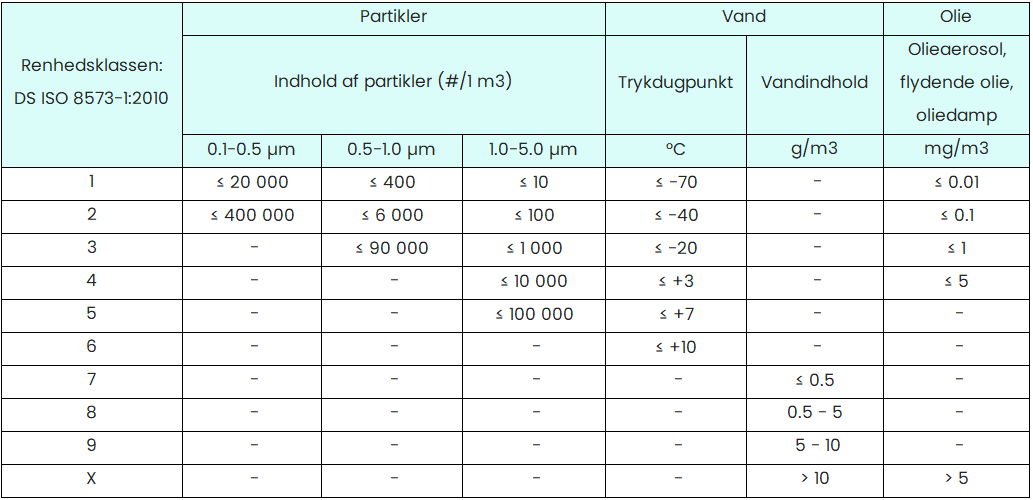
UDPRØVEDE PARAMETRE
PARTIKLER
Målemetode: ISO 8573-4:2019
Måleområde: Måling af partikler i intervallet 0,1-0,5 µm (ISO 8573-1 klasse 1-7)
Måleudstyr: Laserpartikeltæller
VAND
Målemetode: ISO 8573-3:2010
Måleområde: –70 … +30°C
Måleusikkerhed: ±2°C
Måleudstyr: Dugpunktsmanometer
OIL AEROSOL
Målemetode: ISO 8573-2:2007
Måleområde: 0,003 – 2mg/1m3
Måleusikkerhed: ±10%
Måleudstyr: Filtreringssæt , FTIR
MIKROBIOLOGI
Målemetode: ISO 8573-7:2003
Udprøvede parametre: indhold af bakterier, gær og skimmelsvampe i 1m3 luft
Måleudstyr: prøveudtagere til trykluft, kolonikultur
i petriskåle
TEKNISKE KRAV
KONTROLLER FØR DU BESTILLER
FORBINDELSER PÅ KLIENTSIDEN
Hurtigkobling (hun)
Gevind 1/2' eller 3/8' (hun) Slange
6, 8, 10, 12 eller 16 mm (udvendig diameter)
INSTALLATIONSTRYK
Højst 7,3 bar
OMGIVELSESTEMPERATUR
Mindst 10°C
PLACERING AF MÅLEPUNKTET
1.Renset trykluft
Partikeltallet kan kun måles i gas, der er renset på filtrene. Det er ikke muligt at måle før filtrene.
2. let tilgængeligt rum
Måleudstyret er stødfølsomt og vejer mere end 20 kg, så det kan ikke bæres f.eks. op ad en stige, oven på tanke osv.
PRØVETAGNINGSTIDSPUNKT
Det tager ca. 45-60 minutter at gennemføre et sæt test på 1 målepunkt.
rapportering
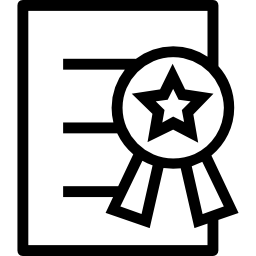
I OVERENSSTEMMELSE MED
GMP-STANDARDEN
Resultaterne anbringes på separate testark (IQ/OQ/PQ). Rapporten indeholder bl.a. identifikation af det anvendte udstyr og de personer, der har deltaget i prøverne.
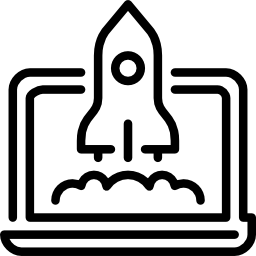
RAPPORTEN LEVERES INDEN
FOR 14-30 DAGE
Vi udarbejder rapporten på engelsk og sender den elektronisk inden for 14 dage (maksimalt 30 dage)
efter målingerne.
EN LANG RÆKKE KUNDER HAR ALLEREDE VIST OS DERES TILLID
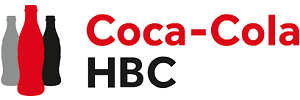
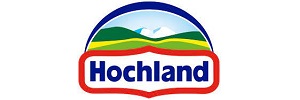
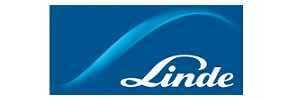
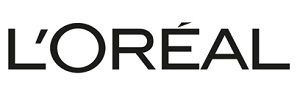
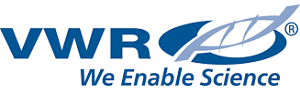
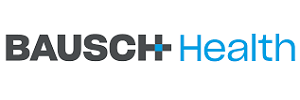
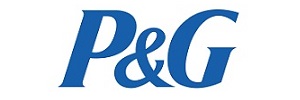
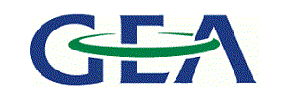
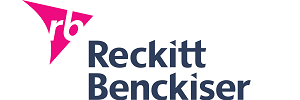
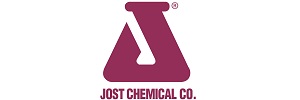
VORES TEAM

Krzysztof ZarczyNski
VALIDERINGSINGENIØR VALIDERING
Ansvarlig for tilbud, udarbejdelse af testplan, gennemførelse af målinger og rapportering af resultater. Uddannet som fødevareteknolog. Erfaring med kvalitetssikring og validering i fødevare- og farmaceutiske produktionsanlæg
info@sigma-lab.dk
[sprog: dansk, engelsk]
+48 530 30 90 30
[sprog: engelsk]
PRISLISTE
Ønsker du et hurtigt overslag over omkostningerne ved at foretage målinger?
I prislisten finder du:
– oplysninger om de målinger, vi foretager
– priser for opmålinger
ISO 8573-4: Indhold af partikler
Partikelindholdet i trykluft er i de fleste industrier den vigtigste parameter, der beskriver trykluftens renhed.
Trykluftrensningsprøvninger udføres normalt for de dele af systemet, hvor trykluften komprimeres:
– kommer i direkte kontakt med produktet/materialet (fødevarer, kosmetik, lægemidler, medicinsk udstyr),
– frigives til omgivelserne og bidrager til partikelantallet i renrummet,
– er forbundet med forureningsfølsomt udstyr (laboratorieapparater, optiske systemer, lasere).
Ved at teste trykluften i 2-3 målepunkter kan der normalt allerede foretages en pålidelig vurdering af trykluftens renhed. Da en laserpartikelmåler ikke kan anvendes til at måle renheden af rågas (der er for mange partikler – resultaterne ligger uden for apparatets måleområde), testes trykluften normalt i slutningen af trykluftfordelingssystemet og eventuelt ved kompressoren, men bag trykluftfiltrene. For at teste trykluft i overensstemmelse med ISO 8573 er det nødvendigt at tilslutte et tryksystem, idet renheden af den gas, der frigives under atmosfæren, ikke kan testes (for de nødvendige typer tilslutning på installationssiden, se nedenfor).
Partikeltællingen foretages ved hjælp af en bærbar laserpartikeltæller, som kan måle partikler så små som 0,1 µm samtidig i fire størrelsesområder: 0,1 – 0,5 µm, 0,5 – 1,0 µm, 1,0 – 5,0 µm og >5,0 µm. Dette gør det bl.a. muligt at bestemme trykluftens renhedsklasse i henhold til kravene i ISO 8573-1 samt at relatere måleresultaterne til kravene i GMP, ISO 14644-1 eller SEMI 49.8. ISO 8573-4:2019 beskriver målemetoden i detaljer – det udstyr, der anvendes til prøvetagning, parametrene for den faktiske måling. For at klassificere antallet af partikler i trykluften i en given renhedsklasse (klasse 1, 2, 3 osv. i henhold til ISO 8573-1) skal partiklerne i hvert af de tre definerede partikelstørrelsesintervaller opfylde kravene i nedenstående tabel.
ISO 8573-serien af standarder tjener kun til at definere renhedsklasser for trykluft, og vi finder ikke grænseværdier (acceptkriterier) for specifikke industrier, der anvender trykluft. I ISO 8573-serien af standarder finder du heller ikke grænseværdier for specifikke anvendelser eller procesforhold inden for en industri. Grundlæggende retningslinjer i denne henseende er blevet offentliggjort af FDA, VDMA, BCAS og BRC. I de fleste tilfælde (fødevarer, kosmetik, lægemidler, laserskæring, elektronikfremstilling, malerværksteder, pulverlakering) forventes tryklufts renhedsklasser (med hensyn til partikelindhold) fra 1 til 4 i henhold til ISO 8573-1. I kritiske anvendelser forventes klasse 1 eller 2. I mange tilfælde anvendes trykluft imidlertid til typiske tekniske anvendelser – den bruges til at styre ventiler, aktuatorer og gribere. I sådanne anvendelser skal forurenende stoffer fjernes fra trykluften for at beskytte pneumatikkomponenter mod korrosion og overdreven slitage. Klasse 3 eller 4 i henhold til ISO 8573-1 er normalt tilstrækkelig her.
ISO 8573-4: Partikelindhold
Faste partikler i trykluft, såsom støv, rust eller andre forurenende stoffer, kan forårsage betydelige problemer, især i applikationer, hvor renlighed er altafgørende. Disse partikler kan beskadige udstyr, forstyrre processer og påvirke kvaliteten af slutprodukter.
Med ISO 8573-4 har virksomheder et stærkt værktøj til korrekt måling af indholdet af faste partikler i deres trykluftsystemer. Standarden specificerer specifikke metoder og udstyr til at sikre, at målingerne er nøjagtige og ensartede.
En vigtig del af standarden er definitionen af partikelstørrelser, der skal måles, og de passende teknikker og instrumenter til hver størrelsesklasse. Ved at følge disse retningslinjer kan virksomheder sikre, at deres trykluft opfylder de ønskede renhedsstandarder, og at ingen uønskede faste forureninger påvirker deres processer eller produkter.
Anvendelsen af ISO 8573-4 er afgørende for industrier som halvlederfremstilling, fødevareforarbejdning og lægemidler, hvor kontrollen med faste partikler er kritisk.
[ISO 8573-4] Spørgsmål til auditøren:
- Er brugeren klar over, at partikelindholdet i trykluften er et vigtigt renhedsparameter?
- Udføres der renhedstest af trykluften i henhold til ISO 8573-4?
- Kommer trykluften i direkte kontakt med produktet eller materialet?
- Bliver trykluften frigivet i et renrum i henhold til ISO 8573-4?
- Er trykluften tilsluttet forureningsfølsomt udstyr i henhold til ISO 8573-4?
- Er der valgt 2-3 målepunkter i overensstemmelse med ISO 8573-4 til vurdering af trykluftens renhed?
- Bruges en laserpartikeltæller til måling?
- Er trykluften testet for enden af distributionssystemet og efter trykluftfiltrene i overensstemmelse med ISO 8573-4?
- Findes der et tryksystem til test af trykluft i henhold til ISO 8573-4?
- Bruges der en bærbar laserpartikeltæller til at måle partikeltallet?
- Kan partikler måles i fire forskellige størrelsesintervaller i henhold til ISO 8573-4?
- Er renhedsklassen for trykluften bestemt i henhold til ISO 8573-1?
- Sammenlignes måleresultaterne med andre standarder som GMP, ISO 14644-1 eller SEMI 49.8?
- Anvendes målemetoden i henhold til ISO 8573-4:2019 til ISO 8573-4-testen?
- Er alle partikelstørrelsesintervaller i henhold til ISO 8573-4 taget i betragtning?
- Bliver ISO 8573-serien af standarder kun brugt til at definere renhedsklasser?
- Er de specificerede grænseværdier for forskellige industrier eller procesforhold i henhold til ISO 8573-4 kendt?
- Overholdes de grundlæggende retningslinjer fra FDA, VDMA, BCAS og BRC i forhold til ISO 8573-4?
- Anvendes renhedsklasse 1 eller 2 i henhold til ISO 8573-1 og ISO 8573-4 til kritiske anvendelser?
- Er den valgte renhedsklasse egnet til tekniske anvendelser i henhold til ISO 8573-4?
- Blev prøveudtagningsmetoderne i henhold til ISO 8573-4:2019 Partikler overholdt?
- Hvilken metode blev valgt i henhold til ISO 8573-4, afhængigt af partikelstørrelsen i trykluftstrømmen?
- Er lysmikroskopmetoden i henhold til ISO 8573-4 blevet brugt til partikler ≥5,0 mikron?
- Er scanningselektronmikroskopmetoden i henhold til ISO 8573-4 blevet brugt til partikler ≥0,005 mikron?
- Er det optiske partikeltælle- og måleapparat blevet brugt i overensstemmelse med ISO 8573-4 til partikler fra ≥0,06 til ≤100 mikron?
- På grund af tidsforbruget blev den tredje metode i henhold til ISO 8573-4 brugt som den mest almindelige prøveudtagningsmetode?
- Blev der ved test med partikeltællings- og måleinstrumenter udført fuld flow-prøvetagning i overensstemmelse med ISO 8573-4?
- Brugte du isokinetiske (partial flow) prøvetagningsteknikker i henhold til ISO 8573-4, hvis fuld flow-prøvetagning ikke var mulig?
- Ifølge ISO 8573-4, hvilket måleprincip blev brugt af instrumenterne?
- Baseret på ISO 8573-4, har man så valgt teknologien med et optisk aerosolspektrometer (OAS) eller en optisk partikeltæller (OPC)?
- Er instrumentet blevet valgt i overensstemmelse med ISO 8573-4 baseret på den partikelstørrelse og koncentration, som brugeren ønsker at måle?
- Er der forskel på de to teknologiers partikelstørrelsesintervaller og koncentrationer i henhold til ISO 8573-4?
- Blev der brugt et OAS-instrument til prøvetagning af ubehandlet trykluft i henhold til ISO 8573-4, som normalt tolererer højere partikelkoncentrationer og større partikelstørrelser?
- Er laserbaserede OPC’er blevet brugt i overensstemmelse med ISO 8573-4 til at detektere små partikelstørrelser ved lave koncentrationer?
- I henhold til ISO 8573-4 blev disse OPC’er typisk brugt til prøvetagning af trykluft efter rengøring af udstyr?
- Hvilke delstrømstestanordninger var påkrævet i henhold til ISO 8573-4?
- Er der anvendt en isokinetisk prøveudtagningsanordning/prøveudtagningsrig i overensstemmelse med ISO 8573-4?
- Er der anvendt en optisk partikeltæller (OPC) i overensstemmelse med ISO 8573-4?
- Opfylder ISO 8573-4-metoden og -udstyret kravene til nøjagtig testning af trykluft i overensstemmelse med renhedskravene i ISO 8573-1 klasse 0, 1 eller 2 for partikler?
- Kan alle OPC’er måles i henhold til ISO 8573-4 i de krævede partikelstørrelsesbånd til ISO 8573-1-klassificering?
- Er det blevet sikret, at den anvendte optiske partikeltæller kan måle i følgende partikelstørrelsesintervaller i henhold til ISO 8573-4: 0,1 – 0,5 μm?
- Kan den optiske partikeltæller i henhold til ISO 8573-4 også måle i partikelstørrelsesintervallet 0,5 – 1 μm?
- Kan den optiske partikeltæller i henhold til ISO 8573-4 også måle i partikelstørrelsesintervallet 1-5 μm?
- Blev der brugt en skiveprøve og lysmikroskopi til prøveudtagning i henhold til ISO 8573-4?
- Blev der brugt en skiveprøve og et scanningelektronmikroskop til prøveudtagning i henhold til ISO 8573-4?
- Er optisk partikeltælling og -måling i henhold til ISO 8573-4 blevet brugt som instrument til prøvetagning?
- Blev lysspredningsmålemetoden brugt til enkeltpartikelmålinger i henhold til ISO 8573-4?
- Er det optiske aerosolspektrometer (OAS) blevet brugt til at tage prøver af ubehandlet trykluft i overensstemmelse med ISO 8573-4?
- Blev der brugt laserbaserede OPC’er i henhold til ISO 8573-4 til prøvetagning efter rengøring af udstyr?
- Blev der brugt isokinetiske prøveudtagningssonder i henhold til ISO 8573-4 til delstrømstests?
- Er de partikeltællere, der er anført i ISO 8573-4, meget dyre?
- Bruges der følsomt testudstyr i henhold til ISO 8573-4?
- Er partikeltællere i henhold til ISO 8573-4 primært egnet til laboratorietest?
- Findes der mange forskellige typer af bærbare partikeltællere, som er i overensstemmelse med ISO 8573-4?
- Er nogle af disse bærbare partikeltællere omkostningseffektive alternativer i henhold til ISO 8573-4?
- Var de fleste bærbare partikeltællere oprindeligt designet til at måle omgivende luft i renrum og ikke-komprimerede trykluftsystemer i henhold til ISO 8573-4?
- Måler mange bærbare partikeltællere ikke op til de værdier, der vises i ISO 8573-1-klassifikationstabellen?
- Kræver mange bærbare partikeltællere, at luften udvides til atmosfærisk tryk i henhold til ISO 8573-4?
- Foretages der ofte partikeltælling i henhold til ISO 8573-4 efter filtreringsudstyr?
- Bliver den såkaldte “valideringstest” af filtre i henhold til ISO 8573-4 ofte diskuteret mellem trykluftbrugere og udstyrsleverandører?
- Er luftbehandlingsanlæg med kompressor ofte mærket “fejl” i henhold til ISO 8573-4, når de faktisk fungerer korrekt?
- Er testinstrumentet ofte ikke ordentligt rengjort og skyllet i henhold til ISO 8573-4?
- Er kalibreringen af testudstyret altid opdateret i henhold til ISO 8573-4?
- Forstår mange ISO 8573-4-operatører ikke, hvordan partikelanalysatoren fungerer?
- Viser nogle ISO 8573-4-testenheder kumulative tællinger, der kan føre til dobbelt eller tredobbelt tælling?
- Kan partikeltællere i henhold til ISO 8573-4 også medtage aerosoler af væsker, kondens og mikroorganismer i deres resultater?
- Måler alle ISO 8573-4-testinstrumenter altid i de 3 bånd, der kræves i ISO 8573-1?
- Er testpunkterne i henhold til ISO 8573-4 ofte efter filtrering og ikke direkte ved udgangen af det endelige filter?
- Er testpunkter, fittings og ventiler ofte identificeret som kilden til meget partikelforurening i henhold til ISO 8573-4?
- Hvor effektive er almindelige og højeffektive tørre partikelfiltre i henhold til ISO 8573-4?
- Er der mange filtre i henhold til ISO 8573-4 i kompressorrummet?
- Er partikeltællinger i henhold til ISO 8573-4 ofte påvirket af forurenende stoffer fra distributionsrørledningen?
- Består rørledninger nedstrøms for filtre til kritisk punktbrug i henhold til ISO 8573-4 ofte af materialer, der kan bidrage til partikeltælling?
- Observeres der typisk et højere partikelantal efter en filterservice i overensstemmelse med ISO 8573-4?
- Kan åbning af filterbeholderen generere partikler i henhold til ISO 8573-4?
- Kan brugen af trykluftsystemet i henhold til ISO 8573-4 påvirke partikeltallet?
- Kan bankning på rørledningen i henhold til ISO 8573-4 løsne partikler og øge partikelantallet?
- Måler mange bærbare partikeltællere typisk kun ned til 0,2 eller 0,3 mikrometer i henhold til ISO 8573-4?
- Kræver mange partikeltællere, at luften ekspanderes til atmosfærisk tryk i overensstemmelse med ISO 8573-4?
- Vedrører dette resultaterne i henhold til ISO 8573-4?
- Fører valideringstest af filtre i henhold til ISO 8573-4 ofte til problemer?
- Bliver fejl ofte tilskrevet filteret i henhold til ISO 8573-4, når de faktisk er ved testinstrumentet?
- Fejlfortolker mange ISO 8573-4-operatører resultaterne, fordi de ikke forstår, hvordan partikelanalysatoren fungerer?
- Forsøger ISO 8573-4-testere ofte at “omfordele” partikeltællinger forkert til ISO-båndene?
- Er partikeltællinger i henhold til ISO 8573-4 ofte påvirket af partikler fra rør og fittings?
- Kan testudstyret vise kumulative tællinger i henhold til ISO 8573-4?
- Kan partikeltællere i henhold til ISO 8573-4 inkludere aerosoler af væsker i deres resultater?
- Kan testudstyret i henhold til ISO 8573-4 også tage højde for kondens og mikroorganismer i sine resultater?
- Bliver testpunkter i henhold til ISO 8573-4 ofte sat op efter filtrering?
- Kan ISO 8573-4-fittings og ventiler ofte forårsage en masse partikelforurening?
ISO 8573-3: Vandindhold (trykdugpunkt)
Tilstedeværelsen af fugt i trykluften er uønsket i de fleste systemer, da kondensering i systemet kan føre til:
- svigt af trykluftsystemets komponenter,
- skader på procesudstyr, der anvender trykluft,
- trykfald i systemet,
- kontaminering af råmaterialer, halvfabrikata og færdigvarer (vand, oxidations-/korrosionsprodukter fra anlægget, mikroorganismer, der finder vækstbetingelser i anlægget med frit vand til stede).
Fugtindholdet i trykluft udtrykkes ved hjælp af parameteren trykdugpunkt. ISO 8573-1 definerer acceptkriterier for fugtindholdet i de enkelte klasser af trykluft netop på grundlag af parameteren trykdugpunkt (se ovenstående tabel).
Dugpunktet, eller mere præcist dugpunktstemperaturen, er den grænsetemperatur, ved hvilken luften når sin maksimale vanddampmætning (relativ fugtighed på 100 %). Yderligere afkøling af luft med en relativ fugtighed på 100 % vil føre til kondensation af vand, der tidligere var transporteret som damp, fordi luften (gassen) ved en lavere temperatur ikke længere kan indeholde så meget vand. F.eks. vil et temperaturfald på 10 °C ved en luftfugtighed på 100 % medføre, at ca. 50 % af den vanddamp, der er til stede i luften, kondenserer. Når vi kender dugpunktet og den temperatur, der i øjeblikket måles i systemet, kan vi derfor vurdere, “hvor langt” vi er fra de betingelser, hvor kondensering af det vand, der er til stede i luften, vil begynde.
For systemer med et arbejdstryk, der er højere end det atmosfæriske tryk, skal udtrykket trykdugpunkt anvendes i stedet for dugpunkt. Trykdugpunktet (°C) angiver trykluftens fugtindhold og bestemmes ud fra den relative fugtighed, temperaturen og arbejdstrykket i trykluftprøvetagningsstedet.
Hvorfor er der overhovedet fugt i komprimeret? Vanddamp vil altid være indeholdt i den atmosfæriske luft, der kommer ind i kompressoren. Ved 24 °C og en relativ luftfugtighed på 70 % vil en 25 hk-kompressor producere ca. 80 liter vand pr. dag. Selv om der normalt er et tørremiddel til stede i trykluftsystemer, vil ethvert tørremiddelsystem have sin begrænsede kapacitet. Der kan især i sommermånederne forventes problemer med at opnå tilstrækkeligt lave fugtighedsværdier for trykluft, da den opvarmede luft indeholder mere fugt end i de køligere måneder, og denne fugt ikke effektivt tilbageholdes i tørretumbleren. Selv om luften opvarmes som følge af kompressionen, hvorved vandet holdes i dampform, afkøles den komprimerede luft, der kommer ind i distributionssystemet, og dampen kondenserer (kondenserer). Som tidligere nævnt vil tilstedeværelsen af kondenseret vand være uacceptabel i mange anvendelser og kan forurene trykluftsystemet og det færdige produkt, hvis trykluften kommer i kontakt med det (fødevare-/kosmetik-/farmaceutisk industri). En parameter, der kan vise, om der er en reel risiko for frit vand i trykluftdistributionssystemet, er måling af trykdugpunktet.
Måling af trykdugpunktet foretages ved hjælp af et bærbart apparat, der er tilsluttet trykanlægget, dvs. at fugtigheden af den trykluft, der frigives under atmosfæren, ikke kan testes (for de krævede typer af tilslutninger på anlægssiden, se nedenfor).
ISO 8573-3: Vandindhold (trykdugpunkt)
Fugt eller vanddamp i trykluftsystemer kan føre til en række problemer, herunder korrosion af udstyrskomponenter, vækst af mikroorganismer og kvalitetsdefekter i slutprodukter. Derfor er det vigtigt at måle og kontrollere fugtigheden.
ISO 8573-3 fokuserer specifikt på testproceduren til måling af luftfugtighed i trykluft. Den giver klare retningslinjer og metoder til at sikre, at vanddampindholdet i trykluft måles nøjagtigt og konsekvent. Disse målinger er afgørende for at afgøre, om trykluften opfylder de specificerede renhedsklasser.
For at kunne måle fugten i trykluft korrekt specificerer ISO 8573-3 specifikke måleinstrumenter og teknikker, der skal bruges. Ved at bruge disse standardiserede metoder kan virksomheder være sikre på at få korrekte og pålidelige data om fugtindholdet i deres trykluft.
For virksomheder, der bruger trykluft i kritiske applikationer, hvor fugt kan være et problem, er det vigtigt at overholde ISO 8573-3. Det giver ikke kun sikkerhed for, at trykluftkvaliteten lever op til standarderne, men det hjælper også med at undgå dyre reparationer eller problemer med produktkvaliteten.
[ISO 8573-3] Spørgsmål til auditøren:
- Er brugeren klar over, at fugt i trykluft er uønsket i henhold til ISO 8573-3?
- Er fugten i dit anlæg skyld i, at komponenter i trykluftsystemet svigter?
- Kan der opstå skader på procesudstyr, der bruger trykluft, hvis du ikke følger ISO 8573-3?
- Oplever du trykfald i systemet på grund af fugt i henhold til ISO 8573-3?
- Er der tegn på produktforurening på grund af kondens i dit anlæg?
- Er trykluftens fugtighedsniveau bestemt af trykdugpunktsparameteren i henhold til ISO 8573-3?
- Opfylder trykluften acceptkriterierne for fugtighed i henhold til ISO 8573-1 og ISO 8573-3?
- Forstår du betydningen og konsekvenserne af dugpunktet i henhold til ISO 8573-3?
- Kan du estimere, hvor tæt du er på kondensforhold baseret på det målte dugpunkt og den aktuelle temperatur?
- Bruger du udtrykket “trykdugpunkt” til systemer med et driftstryk over atmosfærisk tryk i henhold til ISO 8573-3?
- Har du oplysninger om, hvorfor der er fugt i din trykluft?
- Er du klar over, hvor meget vand en kompressor kan producere afhængigt af temperatur og luftfugtighed?
- Har dit trykluftsystem et tørremiddelsystem i henhold til ISO 8573-3?
- Har du bemærket problemer med fugtindholdet i din trykluft i de varmere måneder?
- Er du klar over, at kondenseret vand i trykluften kan forurene systemet og slutprodukterne?
- Bruger du trykdugpunktsmåling i henhold til ISO 8573-3 til at vurdere risikoen for frit vand i dit trykluftsystem?
- Bruger du en bærbar enhed til at måle trykdugpunktet?
- Er du klar over, at fugtigheden i trykluft, der udledes under atmosfære, ikke kan testes i henhold til ISO 8573-3?
- Har du de nødvendige tilslutninger til den bærbare enhed til måling af trykdugpunktet i henhold til ISO 8573-3?
- Har du for nylig udført en trykdugpunktskontrol i dit anlæg i overensstemmelse med ISO 8573-3?
- Arbejder dit testlaboratorium i henhold til de specificerede krav?
- Hvilke prøvetagningsmetoder for luftfugtighed (dugpunkt) er specificeret i ISO 8573-3?
- Bruger du “Full Flow”-metoden til måling af det fulde flow i henhold til ISO 8573-3?
- Er sonden placeret i hovedluftstrømmen i henhold til ISO 8573-3, men beskyttet mod frit vand og andre forurenende stoffer?
- Er sonden inden for de specificerede nedre og øvre grænser for flowhastigheden for målesystemet i henhold til ISO 8573-3?
- Anvendes metoden “Partial Flow Bypass Tube” i henhold til ISO 8573-3 til måling af delstrøm?
- Er sonden installeret i et lille bypass-rør, så flowhastigheden kan kontrolleres?
- Hvis der er tale om bærbart udstyr, er sonden så solidt forbundet med hovedprøvetagningspunktet, og er forbindelsen lavet af et egnet materiale i henhold til ISO 8573-3?
- Hvilket udstyr er nødvendigt til måling af delstrøm i henhold til ISO 8573-3?
- Bruger du et hygrometer, bypass-rør, flowmåler og regulator?
- Har du fundet ud af, om hygrometre med afkølede spejle giver den højeste dugpunktsnøjagtighed, selvom de kan være dyre og følsomme?
- Bruger du typisk hygrometre baseret på modstand, kapacitans eller ledningsevne, da disse giver den bedste balance mellem pris, nøjagtighed, holdbarhed og bærbarhed?
- Er sådanne hygrometre integreret i styringer eller energistyringssystemer i mange tryklufttørrere?
- Måler du luftfugtighed (dugpunkt) enten under atmosfærisk tryk (ADP) eller under systemtryk (PDP) i henhold til ISO 8573-3?
- Specificerer du for hver fugtmåling, om det er ADP eller PDP i overensstemmelse med ISO 8573-3?
- Har du brug for andet udstyr end hygrometeret til at måle luftfugtigheden (dugpunktet)?
- Har du modificeret systemrøret til isokinetisk prøvetagning i henhold til ISO 8573-3?
- Brug prøverør af PTFE eller rustfrit stål til dugpunktsmålinger, især ved lave dugpunkter som -70 °C PDP?
- Har du undersøgt, om visse rørmaterialer er permeable og derfor ikke egner sig til dugpunktsmålinger i henhold til ISO 8573-3?
- Følger du alle de vigtige instruktioner i ISO 8573-3 for at sikre nøjagtige og pålidelige dugpunktsmålinger?
- Er temperaturen på dugpunktet blevet målt i henhold til det specificerede tryk som beskrevet i ISO 8573-3?
- Er luftstrømmen blevet holdt inden for det krævede område for at undgå skader på sensoren og sikre en repræsentativ måling?
- Er sonden i hovedluftstrømmen korrekt installeret og beskyttet mod vand og andre forurenende stoffer?
- Er sonden til en delstrømsmåling blevet placeret i et lille bypass-rør?
- Er sonden blevet placeret i et lille drænrør, der leder luftprøven fra hovedstrømmen til målekammeret?
- Ved målinger ved reduceret tryk, er proben så blevet placeret i et kammer, hvor der strømmer luft fra hovedstrømmen?
- Var målingerne baseret på resultaternes gentagelighed og måleparternes erfaring?
- Påvirker de materialer, der bruges til at lede luften til målesystemet, vanddampindholdet i prøven i henhold til ISO 8573-3?
- Registreres trykket i prøvetagningssystemet under målingen?
- Er temperaturen i prøvetagningssystemet højere end det målte dugpunkt?
- Har målesystemet nået en stabil tilstand før enhver måling?
- Stemmer værdierne fra to på hinanden følgende målinger med mindst 20 minutters mellemrum overens i henhold til nøjagtighedskravene i ISO 8573-3?
- Er der ved målingen taget højde for målesystemets renhed og måleinstrumentets kalibreringskrav?
- Opfylder det anvendte udstyr det krævede konfidensniveau i det respektive måleområde?
- Blev hver målemetode kun brugt inden for det tilladte område af dens anvendelsesgrænser?
- Er referencebetingelserne for fugtighed, især temperatur og tryk i trykluftsystemet, korrekt specificeret i henhold til ISO 8573-3?
- Blev der taget højde for indflydelsen fra andre urenheder i målingen?
- Er den relative luftfugtighed blevet korrekt omregnet til dugpunktet baseret på tabellerne i ISO 8573-3?
- Er måleusikkerheden blevet beregnet korrekt og taget i betragtning?
- Blev måleresultaterne præsenteret i form af trykdugpunktet, og indeholder de de nødvendige detaljer til verifikation i henhold til ISO 8573-3?
- Er temperaturen på prøvetagningsstedet blevet holdt over dugpunktet for den målte gas i overensstemmelse med ISO 8573-3?
- Er kondens blevet undgået i henhold til ISO 8573-3?
- Er der anvendt en elektrisk opvarmningsmetode i overensstemmelse med ISO 8573-3?
- Er prøvetagningsstedet blevet forberedt i overensstemmelse med ISO 8573-3 ved skylning med tør gas?
- Er udstyret blevet opvarmet for at fjerne restvand i overensstemmelse med ISO 8573-3?
- Er tørretiden blevet forlænget i henhold til ISO 8573-3 med et lavere fugtindhold?
- Er hygroskopiske materialer blevet undgået i henhold til ISO 8573-3?
- Er materialer, der afgiver fugt fra organiske eller porøse materialer, blevet undgået i henhold til ISO 8573-3?
- Blev der brugt uigennemtrængelige materialer i overensstemmelse med ISO 8573-3?
- Er brugen af PVC, nylon eller gummi blevet undgået i overensstemmelse med ISO 8573-3?
- Er der udført en overfladebehandling i overensstemmelse med ISO 8573-3 for at forhindre adsorberet vand?
- Var rene miljøer i henhold til ISO 8573-3 at foretrække til fugtmålinger?
- Blev der brugt meget rene rengøringsmidler i overensstemmelse med ISO 8573-3?
- Blev der udført grundig tørring i henhold til ISO 8573-3 efter rengøringen?
- Er længden af prøvetagningsrørene blevet minimeret i overensstemmelse med ISO 8573-3?
- Er rørledningens diameter blevet holdt så lille som muligt i overensstemmelse med ISO 8573-3?
- Er lækager blevet undgået i henhold til ISO 8573-3?
- Er der sikret en passende gasprøveflowhastighed i henhold til ISO 8573-3?
- Er “blindgyder” i rørledningerne blevet undgået i overensstemmelse med ISO 8573-3?
- Er bagdiffusion af fugt blevet minimeret i henhold til ISO 8573-3?
- Blev den psykrometriske metode i henhold til ISO 8573-3 brugt til at måle fugt?
- Blev der brugt et psykrometer i henhold til ISO 8573-3 med to termisk isolerede temperatursensorer?
- Er mokre-sensoren blevet fugtet konstant i henhold til ISO 8573-3?
- Er metoden blevet brugt med et kondenserende spejl i henhold til ISO 8573-3?
- Blev der dannet kondens ved at køle spejlet i den optiske dugpunktsmålemetode i henhold til ISO 8573-3?
- Er der anvendt en elektronisk kondensdetektor i overensstemmelse med ISO 8573-3?
- Er der anvendt en elektrisk fugtighedssensor i overensstemmelse med ISO 8573-3?
- I henhold til ISO 8573-3, ændres sensorens elektriske egenskaber ved vandabsorption?
- Er der brugt et filter til den elektriske sensor i henhold til ISO 8573-3?
- Er der blevet brugt en kapacitiv sensor i henhold til ISO 8573-3 til måling af relativ luftfugtighed?
- Er der anvendt en resistiv sensor i overensstemmelse med ISO 8573-3?
- Er der anvendt en impedansbaseret dugpunktssensor i overensstemmelse med ISO 8573-3?
- Blev der brugt kemiske reaktionsmetoder i henhold til ISO 8573-3 til at måle fugt?
- Blev der brugt et direkte aflæsningsrør i henhold til ISO 8573-3 med kemisk reagerende indhold?
- Blev der brugt spektroskopiske metoder i henhold til ISO 8573-3 til fugtmåling?
ISO 8573-2: Indhold af olie aerosol
Olieindholdet i trykluft er sammen med vand- og partikelindholdet en vigtig parameter, der karakteriserer trykluftens renhed. ISO 8573-2 beskriver metoder til prøvetagning af trykluft, henleder opmærksomheden på elementer til korrekt beskyttelse af prøverne under transport til laboratoriet og beskriver testmetoder til analyse af trykluftens indhold af olieaerosoler. Det resulterende indhold af olieaerosoler anvendes til vurdering af trykluftens renhed – oftest til bestemmelse af den såkaldte ISO 8573-1-klasse for trykluftens renhed.
Bestemmelse af trykluftens olieindhold er et ret kompliceret spørgsmål ud fra et analytisk synspunkt. ISO 8573-1 fastslår, at det samlede olieindhold i trykluft består af olie i flydende form, olie i aerosolform og oliedampe. For at bestemme trykluftens såkaldte olieindholdsklasse skal der tages hensyn til det samlede olieindhold, som er summen af de anførte oliefraktioner. Da olie i aerosolform udgør den største del af olieindholdet i trykluftfiltersystemer (grov, fin, ekstra fin/kulstof), er det almindelig praksis at måle aerosolindholdet af olie i forbindelse med overvågning af trykluftens renhed.
I vores virksomhed anvender vi et prøvetagningssystem i overensstemmelse med ISO-metode 8573-2 punkt B1 – olieaerosolen suges op på et glasfiberfilter og testes derefter i laboratoriet ved hjælp af FTIR-teknologi. Den lave oliekvantificeringsgrænse i denne metode gør det muligt at vurdere trykluftrensningen, selv når der forventes trykluftrensningsklasse 1 i henhold til ISO 8573-1.
Jeg bruger en oliefri kompressor – er der nogen mening med at teste olien i trykluften?
Der er tre kilder til olie i trykluft: aerosoler og oliedampe i den luft, der tages fra omgivelserne for at generere trykluft, olie fra kompressoren (i tilfælde af oliekompressorer) og eksisterende olieforurening på trykluftdistributionssystemets indre overflader (rør, ventiler osv.).
I mange industrier (f.eks. fødevarer, kosmetik, lægemidler) betragtes olie fra trykluft som en potentiel kilde til produktforurening, og gældende lovgivning eller frivillige kvalitetsstyringssystemer (f.eks. BRC, IFS), som producenten har indført, dikterer gennemførelsen af passende risikostyringsmetoder for trykluftforurening. I tilfælde af anvendelse af oliefrie kompressorer er det muligt, at resultaterne af den test af trykluftsystemets olieindhold, som fabrikanten har, vil være et argument for en betydelig reduktion af testhyppigheden i fremtiden eller en reduktion af antallet af tryklufttestpunkter for olieindhold. Det er imidlertid vanskeligt at konkludere, at der ikke er nogen risiko for en bestemt fare, hvis man ikke har nogen af sine egne testresultater i denne henseende for sit eget anlæg.
ISO 8573-2: Indhold af olieaerosoler
Olie i trykluftsystemer kan komme fra kompressorsmøremidler, lækager eller andre kilder. Uanset hvor det kommer fra, kan det være problematisk i mange applikationer, især i fødevare- og medicinalindustrien. Derfor er det vigtigt at overvåge og kontrollere olieindholdet nøje.
ISO 8573-2 giver klare retningslinjer for testproceduren for indholdet af olieaerosoler i trykluftsystemer. Standarden specificerer både det udstyr og de teknikker, der kræves for at måle dette forureningsniveau.
Overholdelse af ISO 8573-2 sikrer, at indholdet af olieaerosoler i et trykluftsystem identificeres og måles korrekt. Dette er afgørende for virksomheder, der ønsker at sikre, at deres trykluft opfylder de specificerede renhedsklasser, og at deres produkter og processer ikke påvirkes af olieforurening.
[ISO 8573-2] Spørgsmål til auditøren:
- Forstår du definitionen af “olie” i henhold til ISO 8573-2?
- Kan du forklare, hvad der menes med “olieaerosol” i henhold til ISO 8573-2?
- Hvad menes der med “wall flow” i forbindelse med ISO 8573-2?
- Er du bekendt med de prøvetagningsmetoder, der er nævnt i ISO 8573-2:2018?
- Hvilket udstyr bruges til metode A-prøveudtagning i henhold til ISO 8573-2?
- Hvilket udstyr er nødvendigt til prøveudtagning i henhold til metode B1 i henhold til ISO 8573-2?
- Hvilket udstyr kræves til prøvetagning i henhold til metode B2 i overensstemmelse med ISO 8573-2?
- Hvilken ISO 8573-2 prøveudtagningsmetode er mest nøjagtig til test efter filtrering?
- Til hvilket kontamineringsområde skal metode A i henhold til ISO 8573-2 anvendes?
- Ved hvilken maksimal temperatur skal metode A i henhold til ISO 8573-2 anvendes?
- Hvor lang tid tager en typisk test med metode A i henhold til ISO 8573-2?
- Til hvilket kontamineringsområde skal metode B1 i henhold til ISO 8573-2 anvendes?
- Ved hvilken maksimal temperatur skal metode B1 i henhold til ISO 8573-2 anvendes?
- Hvor lang tid tager en typisk test med metode B1 i henhold til ISO 8573-2?
- Til hvilket kontamineringsområde skal metode B2 i henhold til ISO 8573-2 anvendes?
- Ved hvilken maksimal temperatur skal metode B2 i henhold til ISO 8573-2 anvendes?
- Hvor lang tid tager en typisk test med metode B2 i henhold til ISO 8573-2?
- Vidste du, at ISO 8573-5 oliedamptest også er påkrævet til validering i henhold til ISO 8573-1:2010?
- Er du klar over, at resultaterne af begge tests skal lægges sammen i overensstemmelse med ISO 8573-2 for at bestemme det samlede olieindhold?
- Hvilken metode i henhold til ISO 8573-2 ville du bruge, hvis der var væggennemstrømning?
- Med hvilken nøjagtighed udføres testene for metode A i henhold til ISO 8573-2?
- Med hvilken nøjagtighed udføres testene for metode B1 i henhold til ISO 8573-2?
- Med hvilken nøjagtighed udføres testene for metode B2 i henhold til ISO 8573-2?
- Ved hvilken maksimal gennemstrømningshastighed i et filter anvendes metode B1 i henhold til ISO 8573-2?
- Ved hvilken maksimal gennemstrømningshastighed i et filter anvendes metode B2 i henhold til ISO 8573-2?
- Hvilken type filter bruges i metode A i henhold til ISO 8573-2?
- Hvilken type filter bruges i metode B1 i henhold til ISO 8573-2?
- Hvilken type filter bruges i metode B2 i henhold til ISO 8573-2?
- Har du den nødvendige viden til at træffe et valg mellem testmetoderne i henhold til ISO 8573-2?
- Er du helt fortrolig med kravene og standarderne i ISO 8573-2?
- Er brugeren af trykluften informeret om olieindholdet som et parameter til karakterisering af trykluftens renhed?
- Er den anvendte metode til udtagning af trykluftprøver i overensstemmelse med ISO 8573-2?
- Er der indført beskyttelsesforanstaltninger for prøver under transport til laboratoriet i overensstemmelse med ISO 8573-2?
- Er testmetoden til analyse af indholdet af olieaerosoler udført i overensstemmelse med ISO 8573-2?
- Hvordan bruges det resulterende olieaerosolindhold til at vurdere trykluftens renhed?
- Bruges ISO 8573-1 renhedsklassen for trykluft til at bestemme olieindholdet?
- Er du klar over, at det samlede olieindhold i trykluft består af olie i væske-, aerosol- og dampform som beskrevet i ISO 8573-1?
- Bliver alle oliefraktioner taget i betragtning ved bestemmelse af trykluftens renhedsklasse med hensyn til olieindhold i henhold til ISO 8573-2?
- Bliver aerosolindholdet i olien målt regelmæssigt?
- Anvendes et prøveudtagningssystem i henhold til ISO-metode 8573-2 punkt B1?
- Bliver olieaerosolen suget op på et glasfiberfilter i henhold til ISO 8573-2?
- Bliver FTIR-teknikken brugt i laboratoriet til at undersøge olieaerosoler?
- Giver den valgte metode mulighed for at bestemme meget lave olieindhold, især hvis der forventes trykluft i renhedsklasse 1 i henhold til ISO 8573-1?
- Hvis der bruges en oliefri kompressor, bliver trykluften så stadig testet for olieindhold?
- Er du opmærksom på potentielle kilder til olie i trykluft, herunder aerosoler, oliedampe og olie fra kompressoren?
- Betragtes olie fra trykluft som en potentiel kilde til forurening i brugerens branche?
- Findes der lovgivning eller frivillige kvalitetsstyringssystemer, der foreskriver passende risikostyringsmetoder for forurening med trykluft?
- Hvis der bruges en oliefri kompressor, er der så overvejelser om at reducere testfrekvensen eller antallet af testpunkter i henhold til ISO 8573-2?
- Findes der egne testresultater vedrørende olieforurening i trykluftsystemet?
- Er hele trykluftfordelingssystemet, inklusive rør og ventiler, blevet kontrolleret for eksisterende olieforurening i overensstemmelse med ISO 8573-2?
- Er du klar over, at metode A i henhold til ISO 8573-2 er egnet til fuldt flow?
- Kontrollerer du, at metode A i henhold til ISO 8573-2 måler både aerosol- og vægstrømningsformer af olie?
- Er metode A i henhold til ISO 8573-2 uegnet til målinger i systemer, hvor ensartet flow, temperatur og tryk ikke kan opretholdes?
- Kan metode A i henhold til ISO 8573-2 bruges på ethvert sted i trykluftsystemet, hvor der forventes høje niveauer af olieforurening?
- Er metode A-testeren i perfekt stand i henhold til ISO 8573-2?
- Undgås bøjninger og albuer inden for rammerne af ISO 8573-2 Metode A?
- Er alle ventiler lukket som foreskrevet i ISO 8573-2 metode A?
- Er trykluftudtagningsstedet indstillet korrekt i henhold til ISO 8573-2 metode A?
- Bruges der en egnet enhed til temperaturregistrering/-måling i henhold til ISO 8573-2 metode A?
- Er der anvendt en egnet enhed til trykregistrering/måling i henhold til ISO 8573-2 metode A?
- Bruges der differenstrykmålere til at bestemme trykfaldet over prøven og backup-filteret i henhold til ISO 8573-2 metode A?
- Er der anvendt en præcist justerbar afspærringsventil i overensstemmelse med ISO 8573-2 metode A?
- Er der anvendt en egnet flowmåler med en nøjagtighed på ± 5 % i henhold til ISO 8573-2 metode A?
- Bruges der en lyddæmper til at begrænse støjen under testen i henhold til ISO 8573-2 metode A?
- Er prøvetagningsfilteret korrekt anvendt og kontrolleret i henhold til ISO 8573-2 metode A?
- Overskrider flowhastigheden gennem prøveudtagningsfilteret ikke producentens anbefaling?
- Er målingerne i henhold til ISO 8573-2 metode A kun gyldige, når filteret har nået steady state?
- Anvendes der et backup-filter i henhold til ISO 8573-2 metode A, som er identisk med prøvetagningsfilteret?
- Er væske opsamlet i prøven eller backup-filteret i henhold til ISO 8573-2 metode A korrekt drænet?
- Er der taget forholdsregler for at kontrollere væskestrømmen, når væsken tømmes?
- Når der udleveres væske, sørger man så i overensstemmelse med ISO 8573-2 metode A for at sikre, at der ikke er luftbobler i den opsamlede væske?
- Lader du væsken bundfælde tilstrækkeligt længe før måling i henhold til ISO 8573-2 metode A, hvis der opstår luftbobler?
- Kan oliens vægt måles direkte i milligram ved vejning i henhold til ISO 8573-2 metode A?
- Bruges der en afspærringsventil til en praktisk forbindelse til testpunktet i henhold til ISO 8573-2 metode A?
- Er trykudtagningsstedet for trykluften korrekt identificeret i henhold til ISO 8573-2 metode A?
- Er der taget de nødvendige forholdsregler for at kontrollere den hurtige luftudledning og forhindre, at den opsamlede olie skummer?
- Er massemåling af olien i henhold til ISO 8573-2 metode A korrekt og angivet i milligram?
- Er udstyret korrekt kontrolleret og opstillet i henhold til ISO 8573-2 Metode A?
- Er trykluftudtagningsstedet korrekt identificeret og anvendt i henhold til ISO 8573-2 metode A?
- Er alle ventiler lukkede, og er testudstyret kontrolleret for lækager i henhold til ISO 8573-2 metode A?
- Forstår du metode B1 og B2 i henhold til ISO 8573-2 til prøvetagning?
- Tillader metode B1 i henhold til ISO 8573-2 kvantificering af olieaerosoler ved konstant flow, forudsat at der ikke er nogen kontaminering af vægflowet?
- Er alle luftstrømme blevet ledt gennem testudstyret via egnede in-line ventiler i overensstemmelse med ISO 8573-2 metode B1?
- Er ventilerne blevet forhåndstjekket i henhold til ISO 8573-2 metode B1 for at sikre, at de ikke bidrager til olieforureningsniveauet?
- Er der lagt særlig vægt på testudstyrets renhed i henhold til ISO 8573-2 metode B1?
- Er der taget højde for yderligere forholdsregler som f.eks. ventilskylning i henhold til ISO 8573-2 metode B1?
- Er den optimale varighed af en testmålingsprocedure blevet bestemt i henhold til ISO 8573-2 metode B1 efter en indledende test?
- Bliver luften ført tilbage til trykluftsystemet i overensstemmelse med ISO 8573-2 metode B1 for at forhindre produkttab?
- I henhold til ISO 8573-2 metode B1, er det så også muligt at udlede flowet til atmosfæren?
- Blev flowmålingen udført i henhold til ISO 8573-2 metode B1 for at bestemme luftmængden under testen?
- Er der taget tydelige forholdsregler i overensstemmelse med ISO 8573-2 metode B1 for at forhindre stødudladninger eller atmosfærisk forurening?
- Er der anvendt en mikroglasfibermembran i overensstemmelse med ISO 8573-2 metode B1 for god målenøjagtighed?
- Opfylder membranen kravene i ISO 8573-2?
- Er opsamlingsmembranen understøttet af et robust, inert materiale i henhold til ISO 8573-2 metode B1?
- Er rørene og ventilerne designet i overensstemmelse med ISO 8573-2 metode B1, så rørenes indvendige diameter er konstant og fri for huller?
- Svarer diameteren på hullet i kugleventilen til rørdiameteren i henhold til ISO 8573-2 metode B1?
- Er aluminium og dets legeringer blevet undgået i overensstemmelse med ISO 8573-2 metode B1 for at forhindre kontakt med opløsningsmidlerne?
- Vidste du, at i metode B2 i henhold til ISO 8573-2 er både hovedrørets flow og prøveflowet nødvendige for at definere testbetingelserne?
- Blev der brugt en prøvetagningssonde i henhold til ISO 8573-2 metode B2?
- Er sonden blevet indsat centralt i hovedrøret i henhold til ISO 8573-2 metode B2?
- Afgiver tætningerne i probe-/holderforbindelsen ikke kulbrinter til opløsningen i henhold til ISO 8573-2 metode B2?
- Holdes lufthastighederne i hovedrøret og i sonden identiske i prøvetagningsperioden i henhold til ISO 8573-2 metode B2?
- Er flowkontrollerne blevet justeret i henhold til ISO 8573-2 metode B2 for at opnå passende aflæsninger på flowmålerne?
- Er nøjagtigheden af prøveudtagnings- og analyseudstyret blevet kontrolleret i henhold til ISO 8573-2 metode B1?
- Blev der brugt tre lag membran i serie i henhold til ISO 8573-2 metode B1?
- Er understøtningens tryktabsreduktion minimeret i henhold til ISO 8573-2 metode B1?
- Er bypass-rørene fleksible i henhold til ISO 8573-2 metode B1?
- Er der udført indledende tests i henhold til ISO 8573-2 metode B2?
- Er alle ventiler lukket ved testens start i henhold til ISO 8573-2 metode A?
- Har du åbnet afspærringsventilen helt for at sætte testudstyret under tryk i henhold til ISO 8573-2?
- Er flowet blevet indstillet til de krævede betingelser via flowreguleringsventilen i overensstemmelse med ISO 8573-2 metode A?
- Har du lukket ventilerne til væskeopsamling i henhold til ISO 8573-2 metode A?
- Arbejder prøveudtagningsfilterelementet i en mættet tilstand i henhold til ISO 8573-2 metode A?
- Er der givet tilstrækkelig tid til at opnå denne tilstand i henhold til ISO 8573-2 metode A?
- Er målingen i henhold til ISO 8573-2 metode A kun blevet foretaget, når prøveudtagningsfilterets differenstryk har nået den stabile del af diagrammet?
- Er der synlig olie i filterglasset på prøvetagningsfilteret i henhold til ISO 8573-2 metode A?
- Indikeres et stabilt trykfald af differenstrykmåleren i henhold til ISO 8573-2 metode A?
- Tager et ubrugt samplingfilter i henhold til ISO 8573-2 metode A længere tid om at nå en stabil tilstand?
- Blev olien drænet fra prøveudtagningsfilteret til måling i henhold til ISO 8573-2 metode A?
- Har du opsamlet den opsamlede olie i henhold til ISO 8573-2 metode A i en egnet volumetrisk måleenhed?
- Har du separeret den opsamlede olie i henhold til ISO 8573-2 metode A for at undgå skumdannelse?
- Har du taget højde for menisken under målingen i henhold til ISO 8573-2 metode A?
- Har du vejet den opsamlede olie i henhold til ISO 8573-2 metode A og registreret massen i milligram?
- Opsamlede det første prøveudtagningsfilter olien i henhold til ISO 8573-2 metode A med den krævede nøjagtighed?
- Blev backup-filteret brugt i henhold til ISO 8573-2 metode A for at sikre, at det første prøvetagningsfilter fungerede korrekt?
- Hvis der er tegn på olie i det andet filter, er det så nødvendigt at udskifte det første filterelement i henhold til ISO 8573-2 metode A?
- Er den kondenserede væske blevet opsamlet i overensstemmelse med ISO 8573-2 metode A i en beholder, der er kompatibel med den opsamlede væske?
- Afhængigt af olietypen, er adskillelsen af olie/vand-emulsionen muliggjort i henhold til ISO 8573-2 metode A?
- Har du drænet det oliefrie vand og derefter tilsat en afmålt mængde opløsningsmiddel for at opløse olien i henhold til ISO 8573-2 metode A?
- Har du drænet den tungere olie/opløsningsmiddel og målt den faktiske mængde opsamlet olie?
- Var det ikke nødvendigt at udsætte testopsamlingskolonnerne for opløsningsmidlet i henhold til ISO 8573-2 metode A?
- Har luftstrømsmålingen i henhold til ISO 8573-2 metode A en nøjagtighed på bedre end 5 % af det faktiske flow?
- Blev temperaturen målt i grader Celsius i henhold til ISO 8573-2 metode A?
- Har temperaturmålingen i henhold til ISO 8573-2 metode A en nøjagtighed på bedre end 1°C?
- Er nøjagtigheden af testen i henhold til ISO 8573-2 metode A afhængig af mængden af opsamlet olie?
- Har du sikret dig, at resultaterne er stabile og reproducerbare i henhold til ISO 8573-2 metode A?
- Hvis mængden af opsamlet olie er målt, er olieindholdet så blevet beregnet i henhold til ISO 8573-2 metode A?
- Er data blevet registreret i overensstemmelse med ISO 8573-2 Metode A og præsenteret i den form, der er specificeret i bilag A til ISO 8573-2?
- Har du brugt formlen i henhold til ISO 8573-2 metode A til at beregne testresultatet?
- Har du truffet alle foranstaltninger for at sikre nøjagtige målinger i henhold til ISO 8573-2 metode A?
- Har du omhyggeligt fulgt alle trin i henhold til ISO 8573-2 Metode A for at opnå nøjagtige og gentagelige resultater?
- Er udstyret blevet korrekt kalibreret og kontrolleret i henhold til ISO 8573-2 metode A før testen?
- Har du fulgt alle instruktioner og protokoller i henhold til ISO 8573-2 Metode A under hele testproceduren?
- Blev alle måleinstrumenter kontrolleret i henhold til ISO 8573-2 metode A før og efter testen?
- Har du sikret dig, at alle instrumenter og alt udstyr fungerer korrekt i henhold til ISO 8573-2 Metode A?
- Har du taget alle nødvendige forholdsregler for at undgå kontaminering eller fejl under testen i henhold til ISO 8573-2 metode A?
- Har du dokumenteret og arkiveret alle resultater og data korrekt i henhold til ISO 8573-2 Metode A?
- Har du taget alle nødvendige skridt for at sikre, at ISO 8573-2 Metode A-testprocedurer overholder standarder og bedste praksis?
- Arbejder du i testlaboratoriet i henhold til kravene i ISO 8573-2 Metode B?
- Er der opretholdt isoterme forhold for at forhindre kondensering af oliedampe i overensstemmelse med ISO 8573-2 metode B?
- Overstiger lufthastigheden gennem membranen ikke 1 m/s i henhold til ISO 8573-2 metode B?
- Overskrider det tryk, der påføres under testen, ikke membranholderens trykkapacitet i henhold til ISO 8573-2?
- Opbevares rene membraner beskyttet mod støv og atmosfærisk forurening?
- Har du brugt en pincet til at indsætte og fjerne membranen i membranholderen i henhold til ISO 8573-2 metode B?
- Er den eksponerede membran blevet opbevaret beskyttet mod støv efter målingen?
- Har du opbevaret membranen i en ren petriskål af glas?
- Er membranen ikke blevet opbevaret i beholdere lavet af organiske eller kulbrinteholdige materialer?
- Blev membranen opbevaret på et køligt sted i henhold til ISO 8573-2 metode B, hvis der gik flere timer mellem måling og analyse?
- Har du tilfældigt udvalgt en ny membran for at sikre, at den er ren i henhold til ISO 8573-2 metode B?
- Er der ingen kulbrinteforurening af membranholderen eller komponenterne ved affedtningsprocedurer i henhold til ISO 8573-2?
- Brugte du polyethylenhandsker efter rengøring af holderen for at beskytte mod fedtforurening fra fingrene?
- Er holderen blevet forspændt med tre lag egnede prøveplader i henhold til ISO 8573-2 metode B?
- Er alt testudstyr fri for olie, kulbrinter og andre forurenende stoffer, før det tilsluttes systemet?
- Bøjninger inden for en afstand af ti rørdiametre blev undgået af måleapparatet?
- Bidrager samlingen ikke til kulbrintebaggrunden, og er dette blevet verificeret ved analyse af opløsningsmidlet?
- Har du udført den indledende testprocedure i henhold til ISO 8573-2 metode B1, når koncentrationen af olieaerosolen er ukendt?
- Blev luften bypasset gennem bypass-røret i henhold til ISO 8573-2 metode B1, før membranen blev indsat?
- Har du forudindstillet det nødvendige flowforhold gennem prøvemembranen?
- Er opsamlingstiden blevet målt i henhold til ISO 8573-2 metode B1, som bør være mindst 2 minutter?
- Har du anbragt membranen i en kulbrintefri beholder og beskyttet den mod forurenende stoffer?
- Er den olie, der er opsamlet på membranen eller i membranholderen, blevet opløst i et egnet optisk opløsningsmiddel?
- Er koncentrationen af olie i opløsningen proportional med absorptionen af IR-lys ved de bølgelængder, der er karakteristiske for olie i henhold til ISO 8573-2?
- Er absorptionen, A, blevet beregnet som specificeret i ISO 8573-2?
- Er absorbansen blevet sammenlignet med grafen over absorbanser for opløsninger med kendt koncentration?
- Har du valgt et opløsningsmiddel, der har god opløselighed for den pågældende olie i henhold til ISO 8573-2?
- Indeholder det valgte opløsningsmiddel ingen C-H-bindinger i sin kemiske sammensætning?
- Har opløsningsmidlet optisk transparens ved de infrarøde bølgelængder i området 3 400 cm-1 til 2 500 cm-1?
- Blev reagenserne håndteret i henhold til producentens eller leverandørens anvisninger i ISO 8573-2?
- Er de valgte opløsningsmidler specielt fremstillet til brug i infrarød spektroskopi?
- Bruger dit laboratorium et dobbeltstråle- eller Fourier-transformeret infrarødt spektrometer i henhold til ISO 8573-2?
- Dækker dit spektrometer et bølgetalsområde på mindst 3.400 cm-1 til 2.500 cm-1 i henhold til ISO 8573-2?
- Har dit spektrometer en transmissionsreproducerbarhed på bedre end 0,3 % i henhold til ISO 8573-2?
- Er membranerne og holderen blevet håndteret og opbevaret korrekt i overensstemmelse med ISO 8573-2 for at forhindre kontaminering?
- Har du sikret dig, at alt udstyr og alle komponenter er blevet ordentligt klargjort og rengjort i overensstemmelse med ISO 8573-2, før du starter testen?
- Har du udført alle de testprocedurer, der er beskrevet i ISO 8573-2 Metode B, korrekt?
- Har du sikret dig, at de anvendte membraner og membranholdere ikke tidligere har været forurenet med olie eller kulbrinter?
- Har du udført analyseproceduren beskrevet i ISO 8573-2 Metode B korrekt?
- Har du opfyldt alle kravene til opløsningsmidler beskrevet i ISO 8573-2 Metode B?
- Er alle nødvendige sikkerhedsforanstaltninger blevet fulgt ved håndtering af de reagenser, der er beskrevet i ISO 8573-2?
- Har du brugt det apparat, der er beskrevet i ISO 8573-2, og opfyldt dets specifikationer?
- Er alle trin i testproceduren blevet omhyggeligt dokumenteret i henhold til ISO 8573-2 metode B?
- Blev alle instrumenter og alt udstyr kontrolleret i henhold til ISO 8573-2 metode B før og efter testen?
- Har du fortolket analyseresultaterne korrekt i henhold til ISO 8573-2 metode B?
- Har du sikret dig, at alle testprocedurer beskrevet i ISO 8573-2 er blevet udført korrekt?
- Har du sikret dig, at testmiljøet og prøveudtagningen i henhold til ISO 8573-2 metode B ikke er blevet kontamineret?
- Har du opfyldt alle de krav til testudstyr, der er beskrevet i ISO 8573-2 Metode B?
- Har du truffet alle nødvendige foranstaltninger for at sikre, at testproceduren overholder kravene i ISO 8573-2 Metode B?
- Har du taget alle nødvendige skridt for at sikre, at resultaterne af testen er pålidelige og nøjagtige i henhold til ISO 8573-2 metode B?
- Arbejder du i testlaboratoriet i henhold til de specificerede krav?
- Bruger du en analysevægt eller et andet præcisionsvejningsinstrument med en opløsning på mindst 0,1 mg i henhold til ISO 8573-2?
- Har du afvejet 100 mg af den olie, der skal analyseres i henhold til ISO 8573-2, og fortyndet den til 100 ml med rent opløsningsmiddel for at opnå volumen?
- Svarer den resulterende stamopløsning til en koncentration på 1 mg/ml i henhold til ISO 8573-2?
- Har du lavet flere kalibreringsprøver fra stamopløsningen, som dækker det forventede oliekoncentrationsområde?
- Blev kalibreringsprøverne fremstillet ved at måle en given mængde stamopløsning og fortynde den til 50 ml?
- Er forberedelsen af kalibreringsprøverne i overensstemmelse med specifikationerne i ISO 8573-2?
- Har du taget højde for, at koncentrationerne i tabel 3 er baseret på, at den målte oliemasse er præcis 100 mg?
- Har du optaget et spektrum for hver kalibreringsprøve og beregnet absorbansen i henhold til 10.1?
- Er der lavet en kalibreringskurve med resultaterne ved at plotte absorbansen mod oliekoncentrationen i henhold til ISO 8573-2?
- Er der udført en lineær regressionsanalyse i henhold til ISO 8573-2 for at konstruere den bedst mulige rette linje?
- Er den beregnede nøjagtighedsværdi, som angivet ved determinationskoefficienten R^2, ikke mindre end 0,995?
- Hvis R^2-værdien er under 0,995, er analysen så blevet gentaget i henhold til ISO 8573-2?
- Er den resulterende kalibreringskoefficient, C, blevet bestemt ud fra kurvens hældning m i henhold til ISO 8573-2?
- Hvis det er muligt, har du så brugt olier af kendt oprindelse fra kompressoren eller en anden kendt kilde til at lave kalibreringsdiagrammet?
- Har du taget højde for, at kalibreringskurven kun er gyldig for den specifikt analyserede olie i henhold til ISO 8573-2?
- Er der etableret en separat kalibreringskurve for hver enkelt olie og også for hver enkelt produktionsbatch af den samme olie i henhold til ISO 8573-2?
- Er olieopsamlingstiderne baseret på den tid, der kræves til olieekstraktion for at opnå opløsninger med et oliekoncentrationsområde på 2 μg/ml til 100 μg/ml i henhold til ISO 8573-2?
- Har du holdt testtiderne korte i starten for at forhindre kraftig forurening af testudstyret i henhold til ISO 8573-2?
- Er olieindholdet, X, blevet beregnet i henhold til ligningen i ISO 8573-2?
- Er A blevet beregnet som absorption i henhold til 10.1?
- Er C blevet bestemt som kalibreringskoefficienten i henhold til kalibreringskurvens hældning m i 11.1 i overensstemmelse med ISO 8573-2?
- Har du observeret luftmængden, udtrykt i liter pr. sekund under referenceforhold, i henhold til ISO 8573-2?
- Er H blevet bestemt som varigheden af testen, udtrykt i timer, i henhold til ISO 8573-2?
- Blev testapparatet brugt som beskrevet for metode B1 og B2?
- Er usikkerheden ved metoden i henhold til ISO 8573-2 bedre end ± 10 % af den målte værdi?
- Er intervallet i henhold til ISO 8573-2 mellem 0,001 mg/m³ og 10 mg/m³?
- Har du overvejet, at måleusikkerheden varierer med en fri luftmængde og prøvetagningstider fra 10 timer til 2 minutter?
- Har du fulgt alle regler og krav i ISO 8573-2 under hele testproceduren?
- Har du sikret dig, at alle dine testresultater overholder kravene og standarderne i ISO 8573-2?
- Arbejder dit testlaboratorium i henhold til de specificerede krav?
- Svarer den generelle opstilling af dit testudstyr til figur B.1 i ISO 8573-2?
- Bruger du den membranholder, hvis design er inkluderet i ISO 8573-2?
- Hvis ikke, bruger du så en kommercielt tilgængelig holder, der bruger den samme cirkulære membran som i ISO 8573-2-holderen?
- Er proben og membranholderen blevet konditioneret til samme temperatur som testluften for at undgå kondens i henhold til ISO 8573-2?
- Er din sonde mindst ti rørdiametre væk fra opstrøms bøjninger eller begrænsninger?
- Og er det tre diametre væk fra de nedstrøms bøjninger eller begrænsninger?
- Påvirker størrelsen af din probe ikke luftstrømmen i henhold til ISO 8573-2?
- Har du taget forholdsregler for at forhindre overfladekondensation af oliedampe?
- Opfylder dine isokinetiske prøveudtagere de turbulente strømningsforhold i henhold til ISO 8573-2?
- Er dit Reynolds-tal mere end 4.000?
- Har dit trykluftsystem et turbulent flow i henhold til ISO 8573-2 under normale industrielle forhold?
- Svarer dit setup til isokinetisk prøvetagning til det setup, der er vist i ISO 8573-2?
- Bruger du kun isokinetisk prøvetagning i systemer med højt flow, når der ikke er noget vægflow?
- Består din testopstilling af de elementer, der er vist i ISO 8573-2?
- Giver din ventil og flowmåler dig mulighed for at justere og måle prøveflowet?
- Følger du retningslinjerne i ISO 8573-2 for dimensionering af de forskellige elementer i membranholderen?
- Tillader designet af membranholderen vist i ISO 8573-2 brugen af en 55 mm membran?
- Svarer den generelle konstruktion af din probe til den, der er vist i ISO 8573-2?
- Er din sonde designet til brug under referencebetingelser ved 700 kPa (7 bar) og en hastighed på 0,16 m/s?
- Bruger du en egnet membranholder til en 55 mm standardskive i henhold til ISO 8573-2 med din probe?
- Har din probe et cirkulært tværsnit med en tykkelse på mindre end 1,5 mm i den åbne ende?
- Har de indvendige og udvendige overflader på din sonde en hældning på højst 30° i forhold til dysens akse?
- Minimerer vinklen på dysen på din probe slagpåvirkningen i henhold til ISO 8573-2?
- Skaber installationen af din isokinetiske prøveudtagningssonde ikke problemer i henhold til ISO 8573-2?
- Har du fulgt det generelle design fra ISO 8573-2 til installation af din sonde?
- Bruger du en simpel kompressionspakning, hvis du antager, at der bruges en fluorocarbon-elastomer (eller lignende) som tætning?
- Forhindrer denne forsegling kontaminering under analyseproceduren i henhold til ISO 8573-2?
- Kan denne tætning holde sonden i røret op til det maksimale driftstryk?
- Giver denne tætning mulighed for at indsætte sonden i røret i forskellige dybder, hvis det er nødvendigt, i overensstemmelse med ISO 8573-2?
ISO 8573-7: Mikrobiologisk prøvning af trykluft
Mikrobiologisk testning af trykluft hjælper med at foretage en vurdering af de mikrobiologiske risici i forbindelse med håndtering af trykluft i kontakt med produkter, der skal fremstilles under hygiejniske forhold – inden for fødevare-, kosmetik-, medicinal- og medicinalindustrien.
Mikrobiologisk prøvning af trykluft behandles i ISO 8573-7 “Trykluft – Del 7: Prøvningsmetode for indhold af levedygtige mikrobiologiske forurenende stoffer”. Testen består i at tilslutte et prøvetagningssystem til trykluftsystemet, at tage en luftprøve i en petriskål med et mikrobiologisk medium og at inkubere den under laboratorieforhold.
I henhold til ISO 8573-1 anvendes indholdet af bakterier, gær og skimmel i trykluft ikke til den grundlæggende klassificering af tryklufts renhed, men er snarere et supplement til denne klassificering. Trykluftkvaliteten skal primært vurderes ud fra tre andre parametre – partikelindhold, vandindhold og olieindhold – og det er udelukkende for disse tre parametre, at ISO 8573-1 definerer renhedsklasser for trykluft og de tilsvarende grænseværdier.
Da risikoen for mikrobiel vækst i trykluftsystemet falder med et fald i trykluftens vandindhold, er det i mange tilfælde muligt at foretage en vurdering af risikoen for mikrobiel vækst på grundlag af en vurdering af trykdugpunktsparameteren.
ISO 8573-1 specificerer derfor ikke grænseværdier for mikroorganismer i trykluft, men kræver blot, at resultaterne for bakterier, gær og skimmelsvampe rapporteres i form af det angivne antal kolonier pr. kubikmeter luft (CFU/m3) ud over den grundlæggende klassificering af trykluftens renhed.
ISO 8573-7: Mikrobiologisk test af trykluft
ISO 8573-7 indeholder en specifik testmetode til bestemmelse af indholdet af levende mikrobiologiske kontaminanter i trykluft. Standarden specificerer både de metoder og instrumenter, der er nødvendige for at måle og kategorisere disse mikroorganismer.
Overholdelse af ISO 8573-7 sikrer, at virksomheder har nøjagtige data om det mikrobiologiske indhold i deres trykluft, hvilket igen hjælper med at forhindre kontaminering og tilhørende sundhedsrisici.
[ISO 8573-7] Spørgsmål til auditøren:
- Er du klar over vigtigheden af mikrobiologisk test af trykluft i henhold til ISO 8573-7?
- Bliver den trykluft, der kommer i kontakt med produkterne, regelmæssigt mikrobiologisk testet i henhold til ISO 8573-7?
- Kender du de specifikke krav i ISO 8573-7 til mikrobiologisk test af trykluft?
- Bruger du et prøvetagningssystem i henhold til ISO 8573-7 til at tage en luftprøve fra trykluftsystemet?
- Er den udtagne luftprøve placeret i en petriskål med et mikrobiologisk medium i overensstemmelse med ISO 8573-7?
- Foregår inkubationen af prøven i henhold til de laboratoriebetingelser, der er specificeret i ISO 8573-7?
- Vidste du, at ISO 8573-1 ikke bruger indholdet af bakterier, gær og skimmelsvampe i trykluft til grundlæggende klassificering?
- Har du kendskab til de tre hovedparametre (partikelindhold, vandindhold og olieindhold) i henhold til ISO 8573-1 til vurdering af trykluftkvalitet?
- Er du klar over, at risikoen for mikrobiel vækst falder i takt med, at vandindholdet falder i henhold til ISO 8573-7?
- Har du allerede foretaget en vurdering af risikoen for mikrobiel vækst baseret på trykdugpunktet, som anbefalet i ISO 8573-7?
- Vidste du, at ISO 8573-1 ikke fastsætter specifikke grænser for mikroorganismer i trykluft?
- Er indholdet af bakterier, gær og skimmelsvampe angivet i din test ud over den grundlæggende klassificering i henhold til ISO 8573-7?
- Angiv resultaterne for bakterier, gær og skimmelsvampe i henhold til ISO 8573-7 i form af det angivne antal kolonier pr. kubikmeter luft (CFU/m3)?
- Har du taget skridt til at sikre, at dine testmetoder er i overensstemmelse med kravene i ISO 8573-7?
- Har du regelmæssige gennemgange og træning for at sikre, at dit team er bekendt med kravene i ISO 8573-7?
- Er den anvendte metode til at verificere tilstedeværelsen af levedygtige mikroorganismer i overensstemmelse med ISO 8573-7?
- Er et agarnæringsstof blevet udsat for trykluftmønsteret i henhold til ISO 8573-7?
- Er der foretaget en kvantitativ vurdering i overensstemmelse med bilag B i ISO 8573-7?
- Er detaljerne for fremstilling af en agarplade i henhold til bilag D i ISO 8573-7 blevet overholdt?
- Blev der brugt en kolonneprøvetager, en type impaktionslufttester i henhold til ISO 8573-7, til delstrømsprøvetagningen?
- Er der udført isokinetisk prøveudtagning af luften i overensstemmelse med ISO 8573-7 og reduceret til det område, der er angivet af producenten?
- Er der udført trykreduktion til atmosfæriske forhold og flowmålinger i overensstemmelse med ISO 8573-7 for at verificere kompatibilitet med producentens anbefalinger eller i overensstemmelse med ISO 8573-4?
- Er tiden for eksponering af agarmediet for trykluftprøven blevet registreret i henhold til ISO 8573-7?
- Er der foretaget målinger for at skelne mellem ikke-mikrobiologiske og mikrobiologiske partikler inden for 4 timer i henhold til ISO 8573-7?
- Har man forsøgt at eliminere væskers indflydelse på partikelstørrelse og antal så vidt muligt i overensstemmelse med ISO 8573-7 for at opnå en korrekt aflæsning?
- Er påvirkningen fra vand i henhold til ISO 8573-7 ikke blevet reduceret ved at opvarme eller tørre luften for ikke at påvirke levedygtigheden af mikrobiologiske organismer?
- Er der taget behørigt hensyn til indflydelsen fra andre væsker end vand i henhold til ISO 8573-7?
- Blev der i ISO 8573-7-testrapporten lavet en erklæring, der bekræftede tilstedeværelsen af levedygtige kolonidannende mikrobiologiske partikler ud over ISO 8573-4-erklæringen for faste partikler?
- Var sætningen “Deklareret sterilitet af trykluft i henhold til ISO 8573-1” efterfulgt af “Steril” eller “Ikke-steril” i henhold til ISO 8573-7?
- Er datoen for prøveudtagningen blevet registreret i overensstemmelse med ISO 8573-7?
- Er datoen for målingerne blevet noteret i overensstemmelse med ISO 8573-7?
- Er placeringen blevet noteret i overensstemmelse med ISO 8573-7?
- Indeholder bilag A i ISO 8573-7 et eksempel på en testrapport?
- Blev metoden i henhold til ISO 8573-4 brugt til at kontrollere tilstedeværelsen af mikroorganismer?
- Er alle de procedurer og krav, der er anført i ISO 8573-7, blevet fulgt korrekt?
- Er kolonneprøveudtagningsmetoden i henhold til ISO 8573-7 blevet anvendt til påvisning af mikroorganismer?
- Er luften blevet ledt gennem et specialdesignet stik i overensstemmelse med ISO 8573-7?
- Blev mikroorganismerne smidt på agaroverfladen efter deres vægt i henhold til ISO 8573-7?
- Er det antaget, at en mikroorganisme fører til en koloni i henhold til ISO 8573-7?
- Kan kolonneprøvetageren bruges til bakterier, gær eller svampe i henhold til ISO 8573-7?
- Har man overvejet særlige metoder til vira og bakteriofager i henhold til ISO 8573-7?
- Roterer en stor agaroverflade (f.eks. en 140 mm petriskål) under et radialt placeret mellemrum i henhold til ISO 8573-7?
- Blev der anvendt aseptiske teknikker i henhold til ISO 8573-7 til prøveudtagningsmetoden?
- Blev et desinfektionsmiddel som f.eks. 70% ethanol anbefalet i henhold til ISO 8573-7?
- Er der taget forholdsregler for at forhindre vækst af mikroorganismer i udstyret i overensstemmelse med ISO 8573-7?
- Blev alle operationer, hvor testudstyret skulle åbnes, udført med mindst mulig forsinkelse i henhold til ISO 8573-7?
- Er der taget forholdsregler mod træk i overensstemmelse med ISO 8573-7?
- Er alt prøvetagningsudstyr blevet steriliseret før brug i henhold til ISO 8573-7?
- Har en testprøve passeret gennem prøveudtagningsudstyret i henhold til ISO 8573-7?
- Blev der udført en blindtest før og efter den faktiske måling i henhold til ISO 8573-7?
- Blev der brugt en 14 cm petriskål med agar i henhold til ISO 8573-7?
- Er der en etiket på petriskålen med oplysninger om sporbarhed i henhold til ISO 8573-7?
- Er der skruet op for lufttilførslen og niveauindikatoren på spalteprøvetageren i overensstemmelse med ISO 8573-7?
- Er indersiden af hulprøvetageren blevet aftørret med en desinfektionspude i henhold til ISO 8573-7?
- Er petriskålen blevet placeret i søjleprøvetageren i henhold til ISO 8573-7, så den radiale linje er direkte under lufttilførselsspalten?
- Blev låget på spalteprøvetageren udskiftet hurtigt, umiddelbart efter at petriskålens låg var blevet fjernet, i overensstemmelse med ISO 8573-7?
- Blev den automatiske prøveudtagning startet ved at trykke på startknappen i henhold til ISO 8573-7?
- Er starttidspunkt, prøvetagningstidspunkt og andre forhold blevet noteret i overensstemmelse med ISO 8573-7?
- Er prøvetagningen afsluttet, når indikatorlampen er slukket, i henhold til ISO 8573-7?
- Er lufttilførslen blevet øget i henhold til ISO 8573-7?
- Er låget på hulprøvetageren forsigtigt blevet løftet i henhold til ISO 8573-7?
- Blev petriskålen taget fra prøvetagningsudstyret i henhold til ISO 8573-7?
- Blev petriskålen forseglet med tape og anbragt i den sterile pose i henhold til ISO 8573-7?
- Er petriskålene blevet inkuberet ved en passende temperatur i henhold til ISO 8573-7?
- Er agaroverfladen fri for kolonier i midten og i yderkanten i henhold til ISO 8573-7?
- Er pladeholderens aktiveringsarm blevet flyttet via mikrokontakten til en ny startposition i henhold til ISO 8573-7?
- Er indersiden af hulprøvetageren blevet aftørret med en desinfektionspude i henhold til ISO 8573-7?
- Hvis der blev foretaget en ny prøveudtagning, blev proceduren så gentaget fra begyndelsen i overensstemmelse med ISO 8573-7?
- Kan en petriskål spores “geografisk” fra producenten til prøvetagningsstedet og til laboratoriet i henhold til ISO 8573-7?
- Viste petriskålen ingen efterfølgende vækst i henhold til ISO 8573-7?
- Blev den mest passende inkubationstemperatur valgt i henhold til ISO 8573-7 tæt på det habitat, hvor mikroorganismerne var til stede før prøvetagningen?
- Blev mesofile bakterier eller svampe dyrket ved temperaturer på 20 °C til 30 °C i henhold til ISO 8573-7?
- Kan andre inkubationstemperaturer overvejes i henhold til ISO 8573-7?
- Kan selektivt medium (agar) bruges til isolering af visse mikroorganismer i henhold til ISO 8573-7?
- Skal optællingen ske inden for en bestemt tidsperiode i henhold til ISO 8573-7?
- Kan ikke-selektive medier testes i henhold til ISO 8573-7 så tidligt som 24 timer efter inkubationens start?
- Skal der foretages regelmæssige observationer i inkubationsperioden i henhold til ISO 8573-7 for at tælle og registrere kolonier?
- Er der truffet foranstaltninger i overensstemmelse med ISO 8573-7 for at forhindre tab af tællepræcision på grund af overdreven vækst af kolonier?
- Udføres prøvetagningen af endotoksiner i trykluft i henhold til ISO 8573-7 ved hjælp af ubrugte plastrør og glasflasker?
- Bliver prøvetagningen af endotoksiner i henhold til ISO 8573-7 udført af erfarent personale?
- Er tilstedeværelsen af endotoksiner i trykluft blevet bestemt ved at måle mængden af gramnegative enterobakterier i kondensatet i henhold til ISO 8573-7?
- Er der foretaget en ekstra måling af indholdet af bakterier, svampe eller gær i kondensatet i overensstemmelse med ISO 8573-7?
- Er proceduren for måling af gramnegative enterobakterier i kondensat i henhold til ISO 8573-7 blevet fulgt?
- Blev der hele tiden anvendt sterile arbejdsmetoder i henhold til ISO 8573-7?
- Er der anvendt en dipstick med et egnet agarmedium i overensstemmelse med ISO 8573-7?
- Er der valgt et testpunkt i trykluftsystemet i overensstemmelse med ISO 8573-7, hvor kondensatet kan opsamles?
- Blev testpunktet desinficeret med 70% ethanol umiddelbart før prøvetagningen i henhold til ISO 8573-7?
- Er låget på røret blevet fjernet med den coatede folie i henhold til ISO 8573-7?
- Blev der taget en kondensatprøve direkte fra testpunktet til det sterile rør i henhold til ISO 8573-7?
- Er låget blevet nedsænket i prøven i 10 sekunder med folien fastgjort i overensstemmelse med ISO 8573-7?
- I henhold til ISO 8573-7, kom folien med begge agaroverflader i tæt kontakt med prøven?
- Blev folien langsomt trukket ud af prøven på ca. 3 sekunder i henhold til ISO 8573-7?
- Er røret blevet tømt i henhold til ISO 8573-7?
- Blev folien omhyggeligt sat tilbage i røret efter podning i henhold til ISO 8573-7?
- Er røret med prøven blevet opbevaret eller transporteret i timevis i henhold til ISO 8573-7, uden at det har påvirket resultatet?
- Er det blevet sikret, at røret med prøven ikke fryser i overensstemmelse med ISO 8573-7?
- Blev filmene inkuberet i henhold til ISO 8573-7 ved +27 °C i op til 14 dage?
- Hvis organismerne vokser meget langsomt, kan inkubationsperioden så forlænges til op til en måned i henhold til ISO 8573-7?
- Blev folien meget omhyggeligt fjernet fra røret efter inkubation i henhold til ISO 8573-7?
- Er vækst- og farvereaktioner blevet undersøgt i henhold til ISO 8573-7 i overensstemmelse med producentens anvisninger?
- Er det acceptable niveau for bakterier, gær og svampe i henhold til ISO 8573-7 10.000 CFU/ml kondensat?
- Hvis der findes en gramnegativ bakterie i kondensatet, er der så endotoksiner til stede i trykluften i henhold til ISO 8573-7?
- Skal den våde del af installationen rengøres og desinficeres i henhold til ISO 8573-7?
- Er dyrkningsmediet blevet afvejet og opløst i vand i henhold til ISO 8573-7 i den mængde, der er angivet af producenten?
- Blev dyrkningsmediet autoklaveret ved 121 °C i 15 minutter i henhold til ISO 8573-7?
- Er dyrkningsmediet blevet justeret til den specificerede pH-værdi i henhold til ISO 8573-7 efter afkøling til ca. +50 °C?
- Blev der brugt sterile 14 cm petriskåle af plast i henhold til ISO 8573-7 til at hælde 65 ml dyrkningsmedium i hver skål?
- Når dyrkningsmediet var køligt og fast, blev petriskålene så pakket i to sterile plastposer i henhold til ISO 8573-7?
- Blev den første pose forseglet med en enkelt dobbelt kuvert i henhold til ISO 8573-7?
- Er den anden pose blevet forseglet med en svejset kant i overensstemmelse med ISO 8573-7?
- Er petriskålen mærket i henhold til ISO 8573-7 med oplysninger om dato, indhold og batchnummer?
- Er prøvetagning af endotoksiner i henhold til ISO 8573-7 en vanskelig proces?
- Kan blot nogle få nanogram endotoksiner i trykluft forårsage sygdom i henhold til ISO 8573-7?
- Skal en måling af indholdet af bakterier, svampe eller gær i kondensatet udføres i overensstemmelse med ISO 8573-7?
- Blev dyrkningsmediet autoklaveret korrekt i henhold til ISO 8573-7?
- Er dyrkningsmediet blevet justeret til den korrekte pH-værdi i henhold til ISO 8573-7?
- Blev petriskålene pakket korrekt og forseglet i plastposer i henhold til ISO 8573-7?
- Er alle trin til klargøring af petriskålene med dyrkningsmedium blevet udført korrekt i overensstemmelse med ISO 8573-7?
ISO 8573-1: Renhedsklasser for trykluft
Trykluft spiller en afgørende rolle i mange industrier. Fra fødevareforarbejdning til elektronikproduktion kan kvaliteten af trykluft have en betydelig indvirkning på produkter, processer og endda medarbejdernes sikkerhed. Der er indført standarder for at sikre, at trykluft er af den højeste kvalitet. En af de førende serier af standarder på dette område er ISO 8573, som specificerer kravene til trykluftens renhed og definerer renhedsklasser til dette formål. Disse internationalt anerkendte standarder giver virksomheder en guide til at måle og sikre kvaliteten af deres trykluft.
ISO 8573-serien af standarder består af ni standarder:
- ISO 8573 Del 1: Urenheder og renhedsklasser
- ISO 8573 Del 2: Prøvningsmetoder for indhold af olieaerosoler
- ISO 8573 Del 3: Prøvningsmetoder til måling af luftfugtighed
- ISO 8573 Del 4: Prøvningsmetode for indhold af faste partikler
- ISO 8573 Del 5: Prøvningsmetoder for indhold af oliedampe og organiske opløsningsmidler
- ISO 8573 Del 6: Prøvningsmetode for indhold af gasformige urenheder
- ISO 8573 Del 7: Testmetode for indhold af levende mikrobiologiske kontaminanter
- ISO 8573 Del 8: Prøvningsmetode for indhold af faste partikler ved massekoncentration
- ISO 8573 Del 9: Prøvningsmetoder for indhold af flydende vand
ISO 8573: Generelle krav
ISO 8573-1 identificerer forskellige typer af forurenende stoffer, der kan forekomme i trykluftsystemer. Disse omfatter faste partikler, vanddamp og olier. Hver af disse typer af forurening kan påvirke den proces, som trykluften bruges til.
Når du etablerer et program til kontrol af trykluftkvaliteten i overensstemmelse med ISO 8573-standarden, er det vigtigt, at du gør dig bekendt med alle dele af ISO 8573-standarden og inkluderer alle de ovennævnte forurenende stoffer i din testplan.
[ISO 8573-1] Spørgsmål til auditøren:
- Er de forurenende stoffer og renhedsklasserne blevet testet i overensstemmelse med ISO 8573 del 1?
- Hvordan blev indholdet af olieaerosoler testet i henhold til ISO 8573 del 2?
- Er testmetoderne til måling af fugt i henhold til ISO 8573 del 3 blevet anvendt?
- Hvilke testmetoder blev brugt til indholdet af faste partikler i henhold til ISO 8573 del 4?
- Hvordan blev indholdet af oliedampe og organiske opløsningsmidler målt i henhold til ISO 8573 del 5?
- Hvilke testmetoder blev brugt til indholdet af gasformige forurenende stoffer i henhold til ISO 8573 del 6?
- Er testmetoderne for levedygtige mikrobiologiske kontaminanter blevet udført i overensstemmelse med ISO 8573 del 7?
- Hvordan blev indholdet af faste partikler testet ved hjælp af massekoncentration i henhold til ISO 8573 del 8?
- Hvilke testmetoder blev brugt til indholdet af flydende vand i henhold til ISO 8573 del 9?
- Er der taget højde for alle relevante dele af ISO 8573-1-standarden i laboratorietestene?
- Er brugeren af trykluft klar over, at ISO 8573 specificerer renhedsklasser for trykluft med hensyn til partikler, vand og olie, uanset hvor i trykluftsystemet luften specificeres eller måles?
- Ved brugeren af trykluft, at ISO 8573 indeholder generelle oplysninger om forurenende stoffer i trykluftsystemer samt henvisninger til andre dele af ISO 8573 til måling af trykluftens renhed eller fastsættelse af krav til trykluftens renhed?
- Har brugeren af trykluft kendskab til, at ISO 8573 identificerer gasformige og mikrobiologiske forureninger ud over de ovennævnte forureninger såsom partikler, vand og olie?
- Er alle relevante aspekter og dele af ISO 8573 blevet overvejet og forstået af brugeren af trykluft?
- Er der specifikke områder i brugerens trykluftsystem, der kræver særlig opmærksomhed med hensyn til renlighed i henhold til ISO 8573?
- Er brugeren af trykluft klar over, hvad en aerosol er i forhold til ISO 8573, og hvordan den opfører sig i et gasformigt medium?
- Ved brugeren af trykluft i henhold til ISO 8573, hvad et agglomerat er, og hvordan det dannes?
- Er brugeren af trykluft klar over, hvad et smøremiddel/kølemiddel bruges til i henhold til ISO 8573?
- Forstår brugeren af trykluft, hvad dugpunktet er i henhold til ISO 8573, og ved hvilken temperatur vanddamp begynder at kondensere?
- Er brugeren af trykluft bekendt med definitionen af kulbrinter i henhold til ISO 8573?
- Ved brugeren af trykluft, hvad mikrobiologiske forureninger er i henhold til ISO 8573, og hvilke enheder de kan bestå af?
- Er brugeren af trykluft klar over definitionen af olie i henhold til ISO 8573 og dens hovedkomponenter?
- Forstår brugeren af trykluft, hvad en partikel er i henhold til ISO 8573?
- Er brugeren af trykluft bekendt med definitionen af partikelstørrelse i henhold til ISO 8573?
- Ved brugeren af trykluft, hvad trykdugpunktet er, og hvordan det hænger sammen med dugpunktet ved et givet tryk?
- Forstår brugeren af trykluft begrebet relativt vanddamptryk eller relativ luftfugtighed i henhold til ISO 8573?
- Er brugeren af trykluft klar over definitionen af damp i henhold til ISO 8573 og dens opførsel under bestemte temperaturer?
- Har brugeren af trykluft fuldt ud forstået alle ovenstående termer og definitioner i forbindelse med ISO 8573?
ISO 8573-1: Renhedsklasser for trykluft
ISO 8573-1 opdeler trykluft i forskellige renhedsklasser. Hver klasse definerer grænser for mængden og størrelsen af faste partikler, vanddampindhold og olieindhold. Disse klasser giver virksomheder mulighed for at vælge den bedst egnede trykluftkvalitet til deres specifikke applikationer.
En omfattende forståelse af kravene i ISO 8573-1 er afgørende for alle, der ønsker at sikre kvaliteten af trykluft i industrielle applikationer. Med denne standard kan virksomheder overvåge, kontrollere og forbedre trykluftkvaliteten, hvilket resulterer i bedre produktkvalitet og et sikrere arbejdsmiljø.
- Er brugeren af trykluft bekendt med referencebetingelserne for gasmængder?
- Kender brugeren referencetemperaturen i henhold til ISO 8573-1 på 20 °C?
- Er brugeren opmærksom på det absolutte lufttryk på 100 kPa eller 1 bar i henhold til ISO 8573?
- Ved brugeren, at det relative vanddamptryk i henhold til ISO 8573 er 0?
- Er brugeren opmærksom på de tre vigtigste forurenende stoffer i trykluft i henhold til ISO 8573?
- Kender brugeren grupperingen af renhedsklasser for trykluft i henhold til ISO 8573?
- Er brugeren bekendt med klassificeringen af forureningskoncentrationer i intervaller i henhold til ISO 8573?
- Ved brugeren, at grænseværdierne for områderne i henhold til ISO 8573-1 er praksisrelaterede?
- Er brugeren klar over, hvordan andre forurenende stoffer skal angives i henhold til ISO 8573-1?
- Forstår brugeren partikelrenhedsklasserne i henhold til ISO 8573-1?
- Kender brugeren målemetoderne for partikler i henhold til ISO 8573-4 og ISO 8573-8?
- Ved brugeren, at klassifikationer fra 1 til 5 i henhold til ISO 8573 ikke kan anvendes, hvis der er partikler, der er større end 5 μm?
- Forstår brugeren renhedsklasserne for fugt og flydende vand i henhold til ISO 8573-1?
- Kender brugeren målemetoderne for fugt i henhold til ISO 8573-3 og ISO 8573-9?
- Er brugeren bekendt med definitionen af oliens renhedsklasser i henhold til ISO 8573?
- Kender brugeren til målemetoderne for flydende olie og olieaerosoler i henhold til ISO 8573-2?
- Kender brugeren betydningen af klasse 3, 4 og X med hensyn til oliedampindhold i henhold til ISO 8573-1?
- Er brugeren klar over, at måling af oliedampe er valgfri, afhængigt af renhedsklasserne i henhold til ISO 8573?
- Ved brugeren, hvilken standard han skal bruge, når han måler oliedamp i henhold til ISO 8573?
- Forstår brugeren, at der ikke er defineret renhedsklasser for gasformige forurenende stoffer i henhold til ISO 8573?
- Ved brugeren, hvor han kan finde repræsentationen af forureningsværdier for gasformige stoffer i henhold til ISO 8573-1?
- Kender brugeren målestandarden for gasformige forureninger i henhold til ISO 8573-6?
- Forstår brugeren, at der ikke er defineret renhedsklasser for mikrobiologiske kontaminanter i henhold til ISO 8573?
- Ved brugeren, hvor han kan finde præsentationen af kontamineringsværdier for mikrobiologiske stoffer i henhold til ISO 8573?
- Kender brugeren målestandarden for mikrobiologiske forureninger i henhold til ISO 8573-7?
- Er brugeren klar over, at renhedsklasserne for trykluft grupperer koncentrationerne af de vigtigste forurenende stoffer i rækker?
- Ved brugeren, at alle andre forurenende stoffer om nødvendigt skal angives direkte med de specifikke tilladte koncentrationer eller bestemmes i trykluftforsyningen?
- Kan brugeren identificere og forstå tabellerne i henhold til ISO 8573-1, som definerer renhedsklasserne for partikler, fugt og olie?
- Er brugeren klar over, at måling af oliedamp skal udføres i overensstemmelse med ISO 8573-5, hvis det skønnes nødvendigt?
- Ved brugeren, at der ikke er defineret renhedsklasser for gasformige og mikrobiologiske forureninger i henhold til ISO 8573?
- Forstår brugeren af trykluft princippet i at markere renhedsklassen i henhold til ISO 8573 på det angivne målepunkt?
- Kan brugeren angive oplysningerne i den angivne rækkefølge og adskilt af et kolon i henhold til ISO 8573?
- Kender brugeren betydningen af “A”, “B” og “C” i forbindelse med renhedsklasserne i henhold til ISO 8573-1?
- Forstår brugeren, hvordan betegnelsen foretages i henhold til ISO 8573, når der ikke er angivet en klasse for et bestemt forurenende stof A, B eller C?
- Kan brugeren bruge bindestregen korrekt til at angive uspecificerede renhedsklasser i henhold til ISO 8573?
- Ved brugeren, hvordan man betegner en forurening i henhold til ISO 8573, hvis den falder i klasse X?
- Kan brugeren korrekt angive den højeste koncentration af det forurenende stof i runde parenteser i henhold til ISO 8573?
- Forstår brugeren den ekstra betegnelse for gasformige eller mikrobiologiske forureninger i henhold til ISO 8573?
- Kender brugeren det korrekte format til at identificere gasformige forurenende stoffer i henhold til ISO 8573-6?
- Kan brugeren angive værdien og måleenheden for forureningen korrekt i henhold til ISO 8573-1?
- Forstår brugeren, hvordan man udpeger andre mulige kontaminanter i henhold til ISO 8573-6?
- Kender brugeren det korrekte format til at identificere mikrobiologiske kontaminanter i henhold til ISO 8573-7?
- Forstår brugeren af trykluft formålet med klassificeringen af luftens renhed i henhold til ISO 8573?
- Er brugeren klar over, at specifikationen af luftens renhed i ISO 8573 vedrører hele trykluftsystemets tilstand og ikke kun individuelle behandlingskomponenter?
- Ved brugeren, at det ikke er muligt at opnå en bestemt luftrenhed ved hjælp af udstyrskombinationer alene?
- Er brugeren opmærksom på vigtigheden af den korrekte smøremiddel-/kølemiddelspecifikation i henhold til ISO 8573?
- Forstår brugeren temperaturstyringens indflydelse på den fysiske tilstand af væsker i systemet i henhold til ISO 8573?
- Er brugeren klar over, at det er nødvendigt at følge vedligeholdelsesintervallerne i henhold til leverandørens anbefalinger for at opretholde luftrenheden i henhold til ISO 8573?
- Er brugeren klar over, at ISO 8573-1 måske ikke er egnet til alle specifikke anvendelser?
- Kender brugeren til eksempler på anvendelser, der kan have særlige krav, som f.eks. åndedrætsluft eller medicinsk luft?
- Er brugeren klar over, at der ved særlige anvendelser skal tages højde for yderligere forurenende stoffer?
- Ved brugeren, hvornår der skal henvises til andre informationskilder som farmakopéer eller renrumsstandarder?
- Forstår brugeren, at nationale krav kan kræve regelmæssig testning for visse applikationer?
- Er brugeren klar over, at forurenende stoffer kan eksistere i fast, flydende eller gasform?
- Forstår brugeren, hvordan forurenende stoffer kan interagere og påvirke hinanden?
- Er brugeren klar over, at faste forurenende stoffer kan komme fra forskellige kilder?
- Kan brugeren estimere størrelsesområdet for faste forurenende stoffer, fra meget store til submikrone?
- Ved brugeren, at faste partikler kan være både inerte og kolonidannende?
- Er brugeren klar over betydningen af partikelklasse 6 og 7 i henhold til ISO 8573?
- Kender brugeren de traditionelle filterstørrelser, der bruges til industrielle værktøjer?
- Er brugeren klar over, at partikelklasse 6- og 7-klassificeringer ikke er absolutte partikelfjernelsesklassificeringer?
- Forstår brugeren effektivitetsvurderingerne for klasse 6- og 7-filtre i henhold til ISO 8573?
- Ved brugeren, at flydende forurenende stoffer hovedsageligt er vand og kompressorsmøremidler/kølemidler?
- Er brugeren klar over, at andre flydende forurenende stoffer kan blive trukket ind i kompressorens indsugningsområde fra den omgivende luft?
- Forstår brugeren, at koncentrationen af flydende forurenende stoffer afhænger af temperatur og tryk?
- Er brugeren klar over, at væsker kan dannes ved kondensation af deres dampe?
- Ved brugeren, at væskeforureninger kan bidrage til korrosion i trykluftsystemet?
- Er brugeren klar over, at væskeforureninger fra kompressorens smøremidler/kølemidler skal være kompatible med tætninger og ikke-jernholdige rør?
- Ved brugeren, at gasformige forureninger hovedsageligt består af vanddamp og damp fra kompressorens smøremiddel/kølemiddel?
- Forstår brugeren, at koncentrationen af gasformige forurenende stoffer afhænger af temperatur og tryk?
- Er brugeren klar over, at andre forurenende gasser kan blive suget ind i kompressorens indsugningsområde fra den omgivende luft?
- Ved brugeren, at gasformige forurenende stoffer kan opløses i tilstedeværende væsker?
- Er brugeren klar over, at gasformige forurenende stoffer kan kondensere til flydende form ved at sænke temperaturen eller øge trykket?
- Kender brugeren de forskellige former for forurenende stoffer i henhold til ISO 8573-1?
- Er brugeren klar over, at det er nødvendigt at kontrollere fysiske parametre som f.eks. temperatur for at opnå en bestemt luftrenhedsspecifikation?
- Ved brugeren, hvordan faste partikler kan klumpe sig sammen i trykluftsystemet?
- Kender brugeren oprindelsen af faste forurenende stoffer i trykluftsystemet?
- Er brugeren klar over, hvilken rolle væskeforureninger spiller i trykluftsystemet?
- Kender brugeren de vigtigste komponenter i gasformige forureninger?
- Er brugeren klar over, at koncentrationen af gasformige forurenende stoffer afhænger af temperatur og tryk?
- Forstår brugeren overgangen fra gasformige til flydende forurenende stoffer?
- Er brugeren klar over, at korrekt styring af parametre som f.eks. temperatur har indflydelse på væskers fysiske tilstand?
Introduktion til ISO 8573-1:2010
ISO 8573-1:2010 er en international standard, der definerer kvalitetsklasser for trykluft. Denne standard er af afgørende betydning for industrier, der anvender trykluft i deres processer, da den giver et fælles sprog for at specificere og måle trykluftens renhed. Standarden fokuserer på tre hovedtyper af forureninger: faste partikler, vand og olie.
For at forstå vigtigheden af denne standard, lad os overveje et praktisk eksempel fra medicinalindustrien. I produktionen af lægemidler er renhed af afgørende betydning. Lad os sige, at en farmaceutisk virksomhed bruger trykluft til at blæse medicinflasker rene før påfyldning. Hvis trykluften indeholder olierester eller partikler, kan det kontaminere medicinen og potentielt skade patienterne. Ved at specificere luftkvaliteten i henhold til ISO 8573-1:2010, for eksempel klasse [1:2:1], kan virksomheden sikre, at:
- Antallet af faste partikler er ekstremt lavt (klasse 1)
- Dugpunktet er tilstrækkeligt lavt til at forhindre kondensation (klasse 2, hvilket svarer til et trykdugpunkt på -40°C)
- Olieindholdet er minimalt (klasse 1, hvilket betyder ≤0,01 mg/m³)
Denne specifikation giver klare retningslinjer for design og vedligeholdelse af trykluftsystemet og sikrer, at luftkvaliteten konsekvent opfylder de nødvendige standarder for sikker lægemiddelproduktion.
Standarden er ikke begrænset til farmaceutisk industri. Den finder anvendelse i en bred vifte af sektorer, herunder fødevareproduktion, elektronikfremstilling, bilindustrien og mange andre. For eksempel i fødevareindustrien, hvor trykluft ofte kommer i direkte kontakt med produkter, er det afgørende at specificere en luftkvalitet, der forhindrer mikrobiel vækst og kemisk kontaminering.
Et andet vigtigt aspekt af ISO 8573-1:2010 er, at den giver mulighed for at specificere luftkvalitet uafhængigt af hvor i trykluftsystemet, målingen foretages. Dette er særligt nyttigt i store, komplekse systemer, hvor luftkvaliteten kan variere på forskellige punkter i distributionsnetværket. For eksempel kan en bilfabrik have forskellige kvalitetskrav til trykluften, der bruges i malerværkstedet (hvor selv små mængder olie eller vand kan påvirke malingens kvalitet) sammenlignet med den luft, der bruges til almindelige pneumatiske værktøjer på produktionslinjen.
For at illustrere dette, lad os overveje et detaljeret eksempel fra en stor bilfabrik:
- Malerværksted: Kræver ISO 8573-1:2010 [1:2:1]
- Partikler: Klasse 1 (≤20.000 partikler i størrelsen 0,1-0,5 µm per m³)
- Vand: Klasse 2 (trykdugpunkt ≤-40°C)
- Olie: Klasse 1 (≤0,01 mg/m³)
- Samlebånd (pneumatiske værktøjer): ISO 8573-1:2010 [3:4:3]
- Partikler: Klasse 3 (≤90.000 partikler i størrelsen 0,5-1 µm per m³)
- Vand: Klasse 4 (trykdugpunkt ≤+3°C)
- Olie: Klasse 3 (≤1 mg/m³)
- Kvalitetskontrol (præcisionsmåleudstyr): ISO 8573-1:2010 [2:3:2]
- Partikler: Klasse 2 (≤400.000 partikler i størrelsen 0,1-0,5 µm per m³)
- Vand: Klasse 3 (trykdugpunkt ≤-20°C)
- Olie: Klasse 2 (≤0,1 mg/m³)
Disse forskellige specifikationer inden for samme fabrik illustrerer fleksibiliteten og præcisionen af ISO 8573-1:2010 standarden. De giver ingeniører mulighed for at designe et trykluftsystem, der effektivt opfylder de varierende krav i forskellige dele af produktionsprocessen, samtidig med at der opretholdes en konsistent og målbar kvalitetsstandard.
Endvidere tillader standarden specificering af yderligere forureningstyper, såsom mikrobiologiske kontaminanter eller specifikke gasser, når det er relevant for applikationen. For eksempel kan en fødevareproducent tilføje en specifikation for maksimalt tilladte kolonidannende enheder (CFU) pr. kubikmeter luft.
I de følgende sektioner vil vi dykke dybere ned i de specifikke aspekter af ISO 8573-1:2010, herunder detaljerede forklaringer af klassifikationssystemet, målemetoder og praktiske overvejelser ved implementering af standarden i industrielle miljøer.
Klassifikation af faste partikler
Trykluft indeholder ofte faste partikler, som kan stamme fra forskellige kilder, herunder atmosfærisk støv, korrosion i rørledninger og slid på kompressorens komponenter. ISO 8573-1:2010 definerer klasser for faste partikler baseret på deres størrelse og koncentration.
Klassifikationssystemet for faste partikler omfatter følgende klasser:
- Klasse 0: Defineres af brugeren, strengere end klasse 1
- Klasse 1 til 5: Baseret på partikelantal pr. kubikmeter for forskellige partikelstørrelser
- Klasse 6 og 7: Baseret på partikelmassekoncentration
Lad os tage et dybdegående kig på klasse 1 som et eksempel:
For klasse 1 gælder følgende maksimale partikelantal pr. kubikmeter:
- ≤ 20.000 partikler i størrelsen 0,1-0,5 µm
- ≤ 400 partikler i størrelsen 0,5-1,0 µm
- ≤ 10 partikler i størrelsen 1,0-5,0 µm
For at forstå, hvad dette betyder i praksis, lad os overveje et eksempel fra halvlederindustrien, hvor ekstremt ren luft er afgørende for produktionen af mikrochips.
Eksempel: Produktion af halvledere
I et renrum til halvlederproduktion kræves der typisk trykluft af klasse 1 eller bedre. Lad os antage, at den ubehandlede trykluft indeholder følgende partikelkoncentrationer:
- 1.000.000 partikler/m³ i størrelsen 0,1-0,5 µm
- 100.000 partikler/m³ i størrelsen 0,5-1,0 µm
- 10.000 partikler/m³ i størrelsen 1,0-5,0 µm
For at opnå klasse 1 kvalitet skal filtreringssystemet have følgende effektivitet:
- For 0,1-0,5 µm: (1.000.000 – 20.000) / 1.000.000 * 100% = 98% effektivitet
- For 0,5-1,0 µm: (100.000 – 400) / 100.000 * 100% = 99,6% effektivitet
- For 1,0-5,0 µm: (10.000 – 10) / 10.000 * 100% = 99,9% effektivitet
Dette kræver et avanceret filtreringssystem, ofte bestående af flere trin:
- Grovfilter til fjernelse af større partikler
- Højeffektivt partikelfilter (HEPA) til fjernelse af fine partikler
- Eventuelt et ULPA (Ultra Low Penetration Air) filter for at opnå den højeste renhed
Beregning af tryktab: Et vigtigt aspekt ved implementering af et sådant filtreringssystem er tryktabet. Lad os antage, at HEPA-filteret har et tryktab på 0,1 bar ved et flow på 100 m³/time. Ved et systemtryk på 7 bar og et totalt flow på 1000 m³/time kan vi beregne energiomkostningerne forbundet med dette tryktab:
Effekttab = Flow * Tryktab = (1000 m³/time * 0,1 bar) / (3600 s/time) ≈ 0,028 kW
På årsbasis (8760 timer) med en elektricitetspris på 1 DKK/kWh: Årlig energiomkostning = 0,028 kW * 8760 timer * 1 DKK/kWh = 245 DKK
Dette illustrerer, at opnåelse af høj luftkvalitet medfører ekstra driftsomkostninger, som skal tages i betragtning ved systemdesign og økonomisk planlægning.
Klassifikation af vand og fugtighed
Vandindhold i trykluft måles typisk ved hjælp af trykdugpunkt eller væskevandsindhold. ISO 8573-1:2010 definerer følgende klasser:
- Klasse 0 til 6: Baseret på trykdugpunkt
- Klasse 7 til 9: Baseret på væskevandsindhold
Lad os fokusere på klasse 2 som et eksempel:
Klasse 2 kræver et trykdugpunkt på ≤ -40°C. Dette er en meget streng specifikation, der ofte anvendes i kritiske applikationer som farmaceutisk produktion eller elektronikfremstilling.
Eksempel: Farmaceutisk produktionslinje
Antag, at vi har en farmaceutisk produktionslinje, der kræver trykluft af klasse 2 for vandindhold. Systemet opererer ved 7 bar og en omgivelsestemperatur på 20°C.
Beregning af vandindhold:
- Mættet damptryk ved -40°C: ca. 12,8 Pa
- Partielt damptryk i trykluften: 12,8 Pa * (7 + 1) = 102,4 Pa
- Vandindhold: (102,4 / (7 * 10^5)) * 1000 = 0,146 g/m³
Sammenlign dette med ubehandlet luft ved 20°C og 50% relativ fugtighed:
- Mættet damptryk ved 20°C: ca. 2339 Pa
- Partielt damptryk: 2339 Pa * 0,5 = 1169,5 Pa
- Vandindhold: (1169,5 / (1 * 10^5)) * 1000 = 11,7 g/m³
For at opnå klasse 2 kvalitet skal tørresystemet fjerne: 11,7 g/m³ – 0,146 g/m³ = 11,554 g/m³ vand
Dette kræver typisk en adsorptionstørrer med regenerering. Lad os beregne energiforbruget for en sådan tørrer:
Antag et luftflow på 500 m³/time og et specifikt energiforbrug på 0,2 kWh/m³ for tørreren: Dagligt energiforbrug = 500 m³/time * 24 timer * 0,2 kWh/m³ = 2400 kWh
Med en elektricitetspris på 1 DKK/kWh: Daglig energiomkostning = 2400 kWh * 1 DKK/kWh = 2400 DKK
Dette illustrerer de betydelige energiomkostninger forbundet med at opretholde en meget lav fugtighed i trykluftsystemer.
Klassifikation af olieindhold
Olieforurening i trykluft kan stamme fra kompressorolie eller fra indsuget atmosfærisk luft. ISO 8573-1:2010 definerer følgende klasser for olieindhold:
- Klasse 0 til 4: Baseret på total oliekoncentration (aerosol, væske og damp)
Lad os fokusere på klasse 1 som et eksempel:
Klasse 1 kræver et totalt olieindhold på ≤ 0,01 mg/m³. Dette er en ekstremt streng specifikation, der ofte anvendes i fødevare- og medicinalindustrien.
Eksempel: Fødevareemballering
Antag, at vi har en fødevareemballeringslinje, der kræver trykluft af klasse 1 for olieindhold. Systemet bruger en oliesmurt skruekompressor, der typisk producerer luft med et olieindhold på omkring 3 mg/m³.
For at opnå klasse 1 kvalitet skal oliefjernelsessystemet have en effektivitet på: (3 – 0,01) / 3 * 100% = 99,67%
Dette kræver typisk et flertrinsfiltreringssystem:
- Cyklonseparator: Fjerner større oliedråber og partikler
- Koalescensfilter: Samler fine oliedråber til større dråber, der kan fjernes
- Adsorptionsfilter med aktivt kul: Fjerner oliedampe og resterende aerosoler
Lad os beregne levetidsomkostningerne for et sådant system:
Antag et luftflow på 1000 m³/time og følgende omkostninger:
- Indkøbspris for filtreringssystem: 50.000 DKK
- Årlige filterudskiftninger: 10.000 DKK
- Årligt energiforbrug pga. tryktab: 5000 kWh
Med en elektricitetspris på 1 DKK/kWh og en levetid på 10 år: Total levetidsomkostning = 50.000 + (10.000 * 10) + (5000 * 1 * 10) = 200.000 DKK
Dette illustrerer de betydelige investeringer og driftsomkostninger forbundet med at opretholde en meget lav oliekoncentration i trykluftsystemer.
Disse detaljerede eksempler og beregninger viser, hvordan ISO 8573-1:2010 standarden anvendes i praksis, og hvilke tekniske og økonomiske overvejelser der er forbundet med at opfylde de forskellige kvalitetsklasser. I næste sektion vil vi se nærmere på, hvordan disse klasser specificeres og anvendes i forskellige industrielle sammenhænge.
Specifikation af luftkvalitet
ISO 8573-1:2010 standarden giver en præcis metode til at specificere luftkvalitet ved hjælp af en kombination af klasser for faste partikler, vand og olie. Specifikationen skrives typisk i formatet:
ISO 8573-1:2010 [A:B:C]
Hvor: A = klasse for faste partikler B = klasse for vand C = klasse for olie
For eksempel betyder ISO 8573-1:2010 [1:2:1]:
- Klasse 1 for faste partikler
- Klasse 2 for vand (trykdugpunkt ≤ -40°C)
- Klasse 1 for olie (total oliekoncentration ≤ 0,01 mg/m³)
Denne notation giver en hurtig og entydig måde at kommunikere luftkvalitetskrav på tværs af forskellige applikationer og industrier.
Avancerede specifikationer
I nogle tilfælde kan det være nødvendigt at specificere yderligere parametre eller afvige fra standardklasserne. ISO 8573-1:2010 tillader dette gennem følgende metoder:
- Brug af “X” klassen: Hvis en forurening overstiger den højeste definerede klasse, bruges “X” efterfulgt af den faktiske værdi i parentes. Eksempel: ISO 8573-1:2010 [1:4:X(5.5)] indikerer, at olieindholdet er 5,5 mg/m³, hvilket overstiger den højeste definerede klasse for olie.
- Specifikation af yderligere forureninger: Andre gasser eller mikrobiologiske forureninger kan tilføjes til specifikationen. Eksempel: ISO 8573-1:2010 [1:2:1] [CO2 < 500 ppm] [0 CFU/m³] Dette specificerer standardklasserne plus et maksimalt CO2-indhold og et krav om ingen detekterbare kolonidannende enheder (CFU) af mikroorganismer.
Lad os se på et konkret eksempel på, hvordan disse avancerede specifikationer kan anvendes i praksis:
Eksempel: Medicinsk gasproduktion
I produktionen af medicinske gasser er luftkvalitet afgørende. Lad os antage, at en producent har følgende krav:
ISO 8573-1:2010 [1:2:1] [CO2 < 300 ppm] [CO < 5 ppm] [SO2 < 1 ppm] [NOx < 2 ppm] [< 0,1 CFU/m³]
Denne specifikation kræver:
- Højeste klasse for faste partikler, vand og olie
- Strenge grænser for specifikke gasser (CO2, CO, SO2, NOx)
- Næsten steril luft med hensyn til mikrobiologisk kontaminering
For at opfylde disse krav, skal trykluftsystemet designes med følgende komponenter:
- Flertrins partikelfiltrering, herunder HEPA-filtre
- Adsorptionstørrer med regenerering for at opnå et lavt dugpunkt
- Katalytisk omdanner til fjernelse af CO og NOx
- Aktivt kul-filtre til fjernelse af olie og SO2
- UV-sterilisering eller membranfiltrering for mikrobiologisk kontrol
Lad os beregne energiforbruget for et sådant system:
Antag et system med et flow på 500 Nm³/time og følgende komponenter:
- Kompressor: 90 kW
- Tørrer: 15 kW
- Filtre og UV-sterilisering: 5 kW
Totalt effektforbrug: 110 kW
Årligt energiforbrug ved kontinuerlig drift: 110 kW * 8760 timer = 963.600 kWh
Med en elektricitetspris på 1 DKK/kWh: Årlig energiomkostning = 963.600 DKK
Dette illustrerer de betydelige energiomkostninger forbundet med at producere luft af meget høj kvalitet.
Praktiske anvendelser i forskellige industrier
Lad os nu se på, hvordan ISO 8573-1:2010 anvendes i forskellige industrier, og hvilke specifikke udfordringer og løsninger der er forbundet med hver anvendelse.
1. Fødevareindustrien
I fødevareindustrien er der strenge krav til luftkvalitet for at forhindre kontaminering af produkter. En typisk specifikation kunne være:
ISO 8573-1:2010 [1:2:1] [< 1 CFU/m³]
Udfordringer:
- Høj luftfugtighed i produktionsområder
- Risiko for mikrobiel vækst
- Behov for oliefri luft i direkte kontakt med fødevarer
Løsninger:
- Brug af oliefri kompressorer
- Adsorptionstørrere med lav regenereringstemperatur
- Sterilfiltrering tæt på anvendelsesstedet
Eksempel: Mælkepulverproduktion
I produktion af mælkepulver bruges trykluft til pneumatisk transport af pulveret. Lad os beregne dugpunktsænkningen, der er nødvendig for at forhindre kondensation:
Antag:
- Omgivelsestemperatur: 25°C
- Relativ luftfugtighed: 60%
- Systemtryk: 6 bar
- Beregn vanddampindhold i atmosfærisk luft: Mættet damptryk ved 25°C ≈ 3169 Pa Partielt damptryk = 3169 Pa * 0,60 = 1901,4 Pa Vanddampindhold = (1901,4 / 101325) * 1000 = 18,76 g/m³
- Beregn nødvendigt trykdugpunkt: For at undgå kondensation skal trykdugpunktet være lavere end den laveste forventede temperatur i systemet. Antag en sikkerhedsmargin på 10°C under omgivelsestemperaturen: Ønsket trykdugpunkt = 25°C – 10°C = 15°C
- Beregn maksimalt tilladt vanddampindhold ved 6 bar: Mættet damptryk ved 15°C ≈ 1704 Pa Maksimalt vanddampindhold = (1704 / (6 * 10^5)) * 1000 = 2,84 g/m³
Dette viser, at tørresystemet skal reducere vanddampindholdet fra 18,76 g/m³ til 2,84 g/m³, en reduktion på næsten 85%.
2. Farmaceutisk industri
I farmaceutisk produktion er kravene til luftkvalitet blandt de strengeste. En typisk specifikation kunne være:
ISO 8573-1:2010 [1:2:1] [< 0,1 CFU/m³] [CO2 < 500 ppm]
Udfordringer:
- Behov for næsten steril luft
- Strenge regulatoriske krav (f.eks. GMP, FDA)
- Kontinuerlig overvågning og dokumentation af luftkvalitet
Løsninger:
- Flertrins filtrering med validerede sterilfiltre
- Avancerede tørresystemer med dugpunktsstyring
- Online overvågningssystemer for partikler, fugt og olieindhold
Eksempel: Beregning af partikelreduktion i et renrum
Antag et renrum klasse ISO 5 (100) med følgende krav:
- Maksimalt 3520 partikler ≥ 0,5 µm per m³
Hvis den indkommende trykluft indeholder 100.000 partikler ≥ 0,5 µm per m³, beregn den nødvendige filtreringseffektivitet:
Effektivitet = (100.000 – 3520) / 100.000 * 100% = 96,48%
For at opnå denne effektivitet kræves typisk et HEPA-filter (H13 eller højere) i kombination med forfiltrering.
3. Elektronik- og halvlederindustri
I produktion af elektronik og halvledere er selv mikroskopiske forureninger kritiske. En typisk specifikation kunne være:
ISO 8573-1:2010 [1:1:1]
Udfordringer:
- Ekstremt lave niveauer af partikler og fugt krævet
- Følsomhed over for statisk elektricitet
- Behov for konstant luftkvalitet 24/7
Løsninger:
- Brug af membrantørrere for at opnå meget lave dugpunkter
- Elektrostatisk neutrale materialer i luftdistributionssystemet
- Redundante systemer for at sikre konstant forsyning
Eksempel: Beregning af partikelfjernelse i et renrum for halvlederproduktion
Antag et renrum klasse ISO 3 med følgende krav:
- Maksimalt 35 partikler ≥ 0,5 µm per m³
Hvis den indkommende trykluft indeholder 100.000 partikler ≥ 0,5 µm per m³, beregn den nødvendige filtreringseffektivitet:
Effektivitet = (100.000 – 35) / 100.000 * 100% = 99,965%
Denne ekstremt høje effektivitet kræver brug af ULPA-filtre (U15 eller U16) i kombination med flere forfiltre og muligvis elektrostatisk partikelfjernelse.
Disse eksempler illustrerer, hvordan ISO 8573-1:2010 standarden anvendes i praksis i forskellige industrier, og hvilke tekniske udfordringer og løsninger der er forbundet med at opfylde de strenge krav til luftkvalitet. I næste sektion vil vi se nærmere på, hvordan man designer og optimerer trykluftsystemer for at opfylde disse krav på en energieffektiv måde.
sigma-lab.dk er et mærke, der ejes af Biuro Naukowo-Techniczne SIGMA, Jezycka 44a/5, 60-865 Poznan, Polen.
VAT ID: PL6661925548
Kontakt
-
Email:
info@sigma-lab.dk
[sprog: dansk, engelsk]
Telefon:
+48 530 30 90 30
[sprog: engelsk]